Discover all the members of the 8H Triacs series
To improve the accessibility of our content, please find the audio version of this blog post.
ST is announcing a new milestone with the availability of 15 part numbers in its series of 8H Triacs, rated at 800 V, which all support a junction temperature of 150 ÂşC. The family of devices now ranges from 8 A to 30 A for a wide gamut of applications. The components are also available in TO-220AB, TO-220AB Ins, and D2PAK packages. The latter offers better integration and dissipation, enabling engineers to cut heatsinks by half compared to a TO-2 package.
The expansion of our 8H Triacs series is a direct response to new industry challenges. Indeed, the components address recent desires to shrink the circuit and its enclosure while keeping high operating temperatures. These seemingly contradictory requirements demanded new solutions like our new 8H Triacs, which already received design wins. Let us, therefore, look at the new electrical obstacles engineers face and what they can do to solve them.
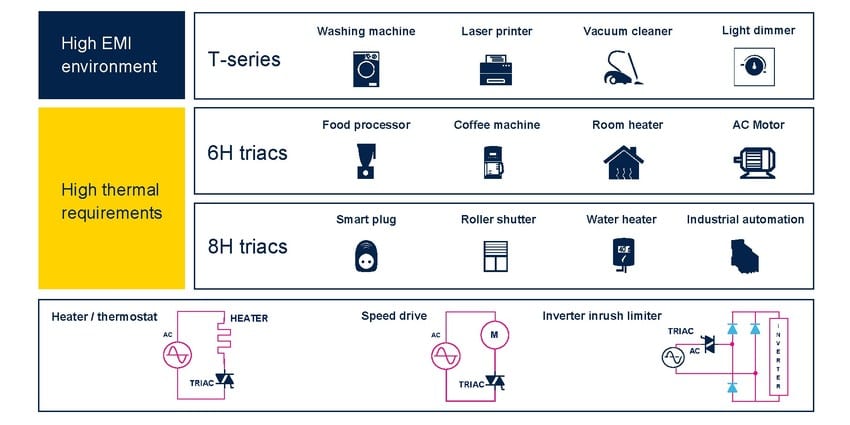
8H Triacs and The New Challenges Engineers Face
Smaller but More Powerful
Let’s take the classic example of the hairdryer. First invented by a French stylist in 1890, the device looked like an inverted vacuum cleaner and was almost as tall as a person. American companies then innovated, releasing the first handheld model around 1915. It weighed about 2 lbs (1 kg) and could only produce 100 W of heat. Today, a standard model weighs half that, is far safer, and offers nearly 2,000 W. Despite these accomplishments, the industry is still moving toward smaller and more powerful appliances. Each technological leap is no longer as drastic as it was in the 1900s. Yet, water heaters, coffee machines, or hair dryers are still shrinking to fit smaller living spaces, reduce their environmental impacts, and more.
Safety Challenges
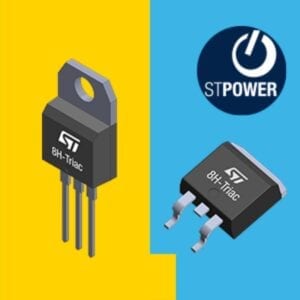
The inherent problem behind smaller hair dryers is that they still have to operate at high temperatures. Similarly, a coffee machine or water heater must still provide enough heat to reach a boiling point. However, shrinking the overall systems creates new electrical challenges that can have damaging consequences. In the case of a household blender, shrinking the overall design cannot come at the cost of safety measures. For instance, blenders almost always include a damping protection circuit against fast transient voltages at the mains. Without it, a machine in the off-state, but still plugged to the wall, could suddenly run because of a sudden current surge, which is potentially harmful. However, protection circuits don’t always easily scale down.
The Importance of the Junction Temperature
ST’s 8H Triacs now withstand higher fast transients and support a junction temperature of 150 ÂşC, which means that it is possible to more efficiently and safely shrink designs. Indeed, at first glance, being able to reach 150 ÂşC instead of 125 ÂşC may not appear that impressive. However, assuming that engineers are looking to keep the surface temperature of the device at about 60 ÂşC, the improvement signifies that instead of benefitting from a margin of 65 ÂşC (125 – 60), engineers now get to enjoy a headroom of 90 ÂşC. It’s this increase of 50% that enables them to cut the heatsink by two.
8H Triacs and the New Solutions Now Available
Greater Temperature, Smaller Designs, Higher Reliability
Beyond the junction temperature itself, engineers also study the range of products from a manufacturer that offer such thermal specifications. For instance, there are ST 8H triacs for smaller devices (8 A), water heaters (10 A), and even industrial HVACs (30 A), which is a sign of the reliability of the underlying manufacturing processes. Additionally, having a broad range of loads may help a company hasten the qualification process since devices all use a similar architecture.
Another specification engineers study closely is the maximum on-state voltage drop (VTM). It measures the voltage across the devices when it is on. The value is important because it directly impacts the size of other cooling components and, therefore, the design’s dimension. On a device like the T1635H-8G, a 16 A — 800 V 8H Triac, the maximum VTM is only 1.5 V at 22 A and 25 ºC. Similarly, the 8H Triacs have a lower leakage current at 150 ºC, which means the device is more stable over time and runs cooler in off state.
Don’t Forget Robustness
When choosing a device, teams finally delve into its robustness. Standards are increasingly more stringent. Customers demand even more from their final product. And a design with high reliability and a long lifespan can propel a brand to new heights. Hence, to better assess a component’s robustness, engineers must look at its noise immunity. Teams ought to also check the minimum rate of change in voltage that would unwantedly turn the device on (dV/dt) and its turn-off commutation capability ((dI/dt)c). With a noise immunity of up to 6 kV in applicative circuit, a static dV/dt of 2,000 V/µs at 150 ºC, and a solid (dI/dt)c of at least 25 A/ms for our 30 A devices, the 8H Triacs have a unique advantage that already led to design wins.