When people see that it’s possible to power an STM32U0 using only a printed organic photovoltaic module from Dracula Technologies—without a battery or a USB cable connected to a PC—many will wonder how it’s even possible. After all, Arthur Clarke said it best, “Any sufficiently advanced technology is indistinguishable from magic.”
However, this is precisely what we demonstrate in the video below. Thanks to the ultra-low power consumption of the STM32U0 and the energy-harvesting capabilities of Dracula Technologies’ indoor organic photovoltaic cells, it’s possible to store enough energy in a capacitor to run an MCU application that reads data from sensors. In the demo, ST and Dracula Technologies display the sensor data on a screen and transmit it via the S2-LP (sub-1 GHz transceiver).
Dracula: A new power source
What is the LAYER® organic photovoltaic module?
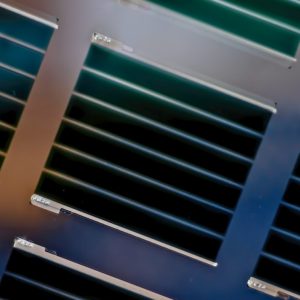
Dracula Technologies, a member of the ST Partner Program, is behind the LAYER organic photovoltaic (OPV) module, which uses an inkjet printing technology to produce light-absorbing cells. From this comes LAYER®Vault, a 2-in-1 solution that combines energy harvesting (on the front) and storage (on the back) on a single, flexible film. Just a few weeks ago, Dracula Technologies launched an upgraded version of its LAYER® OPV module, improving energy efficiency by 15%. This advancement allows device manufacturers to either use a smaller module or achieve greater power output with a module of the same size. Dracula Technologies achieved this by replacing copper bus bars with smaller silver ones that opened the way For larger photovoltaic cells.
How much light does LAYER need?
LAYER, an acronym for Light As Your Energetic Response, is so efficient that it can harvest enough energy from indoor ambient light only. In practice, it generates energy with as little as 5 lux, or about a 0.5 foot-candle, which is the equivalent of a very dim room. Additionally, the inkjet printing process enables a significantly wider range of shapes. Dracula Technologies often showcases modules looking like a bat, but concretely, it means engineers can optimize designs to fit tight spaces or other unique environmental constraints. The modules are also about 0.3 mm thin and flexible, which further helps the integration process. For instance, it’s very common to see LAYER wrapped around the device it powers.
Why is LAYER so flexible?
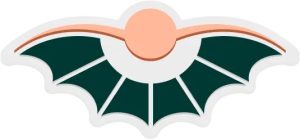
To achieve such a high level of flexibility, Dracula Technologies uses an inkjet printing process to deposit multiple layers, including the photoactive one. The company prints four layers, one on top of the other, at low temperatures, ensuring highly uniform and precise patterns thanks to a nozzle just a few micrometers wide. The printhead deposits the ultra-thin layers onto a thin, flexible plastic film, which gives the module its excellent physical flexibility. Notably, the inks used by Dracula Technologies are free from heavy metals and rare earths, unlike traditional thin-film photovoltaic panels that use tellurium, cadmium, or indium.
A new source of power
Is it difficult to use an STM32U0 and LAYER together?
The demo in the video above was made possible thanks to the close collaboration between ST and Dracula Technologies. Interestingly, we were able to put the demo together in only a couple of months, which is a testament to the ease of use and straightforward aspect of this partnership, and probably one of the most overlooked benefits of LAYER coupled with an STM32 MCU. Indeed, when paired with the STM32U0, using the OPV just works. And when Dracula Technologies decided to develop their custom PCB featuring the ST MCU, it took their trainee only six months, starting from the schematics of the Nucleo board all the way to the final evaluation kit that the company is now offering.
How can the STM32U0 run only on LAYER?
In a nutshell, using LAYER with the STM32U0 is about finding the right balance between energy accumulation and power consumption. At first, the module simply needs to charge the capacitors to offer a minimum of 1.6 V. When that happens, the STM32U0 runs a very rapid boot sequence and enters its low-power STOP 2 mode. In this state, most of the VCORE domain enters a low-leakage mode, while the content of the SRAM and registers remains in memory, and developers may choose to keep the real-time clock active. It’s also possible to keep the voltage monitor as well as specific interfaces and timers active.
This is one of the key features of the STM32U0 because STOP 2 mode consumes very little despite all this. In the case of the application running on the LAYER OPV module, developers set up a STOP 2 mode with a current of less than 1 µA. And since the STM32U0 can operate certain functions while using an input voltage of less than 3 V, the system will initialize peripherals and the clock gradually. Concretely, the MCU waits for the capacitor to deliver about 3 V, then it sets up certain features, then goes back to STOP 2, waits for the capacitor to charge, and continues the initialization process.
Once the MCU is fully initialized, the program waits for the tiny capacitor to be fully charged, meaning that it can deliver 3.4 V. When that’s the case, the power voltage detector throws an interrupt, which wakes the MCU. The STM32U0 then reads data from the onboard sensor, sends the result to the display, and then goes back to sleep. The overall process demands so little power that it’s possible to execute this runtime every second and never run out of power, as long as the LAYER is still harvesting energy. And since the power supply is more straightforward than in traditional settings, engineers don’t need a power management IC, which will also help lower the bill of materials.