Before emission-free electric vehicles fill our roads, there are a number of improvements that car makers can make to internal combustion engines to reduce emissions while they continue to bear the burden of most of the world’s transport needs.
Gasoline direct injection (GDI) combustion with lean stratified operation reduces toxic engine emissions and achieves significant benefits in fuel consumption. So far so good. However, using the precise high air/fuel ratio for lean stratified operation can also have some disadvantages, including engine instability, power loss and increased nitrogen oxide (NOx) emissions. Using multiple gasoline injection strategies can minimize these problems. But, these strategies require the delivery, via the injectors, of very small amounts of fuel, in very accurate doses. And then there is an engineering problem too: to deliver the very small amounts of fuel, traditional solenoid injectors are forced to work in their “ballistic” region, where the correlation between coil energizing time and injected fuel amount becomes highly non-linear!
The engineers at STMicroelectronics targeted a solution that could manage ballistic injections and ensure, using multiple-injection strategies, optimal engine functioning throughout the entire range of engine operating conditions.
The two key issues to overcome were to minimize the lean fuel-mixture drawbacks of higher NOx emissions and engine instability from the higher oxygen content in the lean mixture and spray “wall impingement” when the sprayed fuel contacts the colder cylinder wall and causes instability and higher particle emissions. To overcome these issues with multiple injections strategy required mastering the ballistic mode of the solenoid injectors to provide controlled fuel injections with maximum precision.
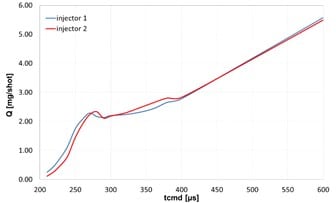
Ballistic Mode
As the figure on the left shows, two injectors from the same family demonstrate good linearity for solenoid command pulse widths greater than 400µs (>2.8mg of fuel). Unfortunately, for multiple injections, the pulses need to be less than 400µs in the very non-linear region. This non-linearity is due to many hard to improve electro-mechanical issues including injector spring-mass inertia, electromagnetic force exerted by the coil and friction variations between solenoids.
To master the desired injection targets and to extend the use of solenoid injectors to short injections, we needed real-time information about the actual fuel amount delivered during ballistic operation. With this information, we could adjust in real-time the injector energizing time using a closed-loop algorithm to obtain the optimal injected fuel quantity.
How is this possible?
In our labs, we found that the injection voltage signal correlates with the actual quantity of fuel delivered. The graph below illustrates a comparison between the injector voltage signal in orange and the corresponding injected fuel mass flow in grey.
By analyzing the two curves, we found that there was no solenoid opening delay, 0s in our graph. However, the voltage signal shows an inflection at the same time as the injected mass flow rate is annulled (the yellow dotted line). This time corresponds to the injector needle closing time, which occurs during the switch-off phase, when the injector coil is de-energized and a self-induction voltage is created.
By monitoring the injector control voltage signal in real-time, we could calculate the amount of fuel injected while in ballistic mode. We could then compare the injected fuel amount with the desired target fuel mass value previously defined and loaded in the engine control maps. From this comparison, we could define and implement a correction value for the coil energizing time.
By using this control strategy, GDI solenoid injectors can be used for very short injections, when ballistic behavior occurs, enabling their use in multiple injection strategies for GDI engines.
Comparison between differential voltage command signal and the corresponding injected mass flow rate, for a coil energizing time of 300 µs.
A Complete Product Range
STMicroelectronics has a complete product range for the full electronic control of the next generation of GDI engines. It includes devices able to manage ballistic injections and ensure, using multiple-injection strategies, an optimal engine functioning in the entire range of engine operating conditions. ST is making Driving Smarter and Greener.
To find out more about ST’s Engine Management solutions click here
STMicroelectronics devices for electronic control of the next generation of GDI engines.