The LPS22DF pressure sensor is officially receiving the NextNav certification today, which guarantees performance and reliability for geolocation and other types of applications. The qualification thus delivers new assurances to an increasing number of makers needing precise vertical positioning information for regulatory or market reasons. We already covered the LPS22DF in a blog post last year. The device supports a maximum pressure of 1,260 hPa while only consuming 9.4 µA in high-performance mode. Hence, the NextNav certification serves as an objective and external recognition of its capabilities, encouraging makers to adopt it.
The challenge of meeting new requirements for 911 calls
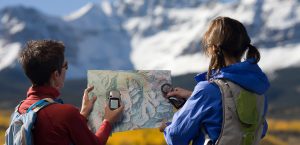
On March 2018, the United States Congress passed the RAY BAUM’S Act, which, among other things, mandates that “dispatchable location” information include details such as floor levels or room numbers when dialing 911. The goal was to ensure that emergency services could rapidly respond, whether the caller used a landline, cellphone, VoIP, or other technologies. One way the FCC (Federal Communications Commission) implemented these new regulations was through its Enhanced 911, which set new standards for accuracy in latitude, longitude, and vertical positioning.
Consequently, the network provider must transmit more information to Public Safety Answering Points (PSAP), which receive the 911 call, and a voice-capable device must gather it. While PSAP and networks have been updated, the last holdout was the consumer device making the call. Regulators have started mandating that as of 2021, all voice-capable systems must meet the requirements set by the RAY BAUM’S Act and the FCC. Makers must, therefore, rapidly meet this new challenge if they want to operate in the United States. One of the issues was to show that their phones, tablets, smartwatches, IoT devices, and other voice-capable products were accurate enough to meet the new standards. That’s where NextNav comes in.
NextNav Certified is a program established by NextNav to ensure that devices, applications, and solutions meet specific requirements to utilize their technology effectively, such as E911 devices. This certification ensures that products and services integrate seamlessly with NextNav’s vertical positioning location services and have undergone rigorous testing to meet performance benchmarks. A NextNav certification thus demonstrates that a product is reliable, accurate, and compatible with NextNav’s technology.
Beyond devices and applications calling emergency services, new systems are also seeking NextNav certifications. For instance, WiFi 6E/7 devices use pressure sensors to establish a precise vertical position and thus ensure a maximum access point (AP) power mode and coverage. A NextNav certificate often plays a role in helping a company decide whether to qualify one device over another for a specific application. New network devices also use such MEMS to report their location. Put simply, accurate and reliable pressure sensors like the LPS22DF are opening the door to new use cases in consumers and industrial markets, to only name a few.
What makes the LPS22DF special?
Its packaging
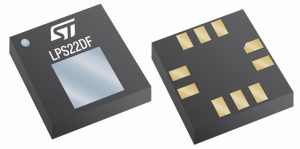
If the LPS22DF received the NextNav certification, it’s because the device has characteristics that stand out. For instance, it has a unique full-molded package to ensure dust and mold resistance. While traditional packages use a cavity, ST uses microscopic holes much smaller than the traditional 20 µm dust particles. Consequently, the device lets the air through, but it isn’t sensitive to the degradation caused by dust thanks to the microscopic holes and a silicon cap protecting the sensing membrane. In fact, the package can withstand such dusty environments it qualifies for the JEDEC J-STD-020 standard. As a result, makers can use the device in many manufacturing settings without worrying that the dust will damage it.
Its architecture
Another feature that makes the LPS22DF unique in the industry is the ability to incur less drift while showcasing faster recovery after soldering. This is a critical aspect because, traditionally, the extreme heat needed during the soldering process significantly disrupts the MEMS’s accuracy. Consequently, manufacturers must proceed to extensive calibration operations, which adds to the overall time and costs. The LPS22DF is different because it embeds a unique MEMS design that reduces the drift significantly and accelerates the recovery after soldering. In certain settings, makers could even do away with a recalibration after soldering. Additionally, the LPS22DF’s design provides long-term stability by limiting the drift over time.
Its ecosystem
The best way to experiment with the LPS22DF is to grab the STEVAL-MKI224V1, a daughter board for the X-NUCLEO-IKS01A3 or the STEVAL-MKI109V3. Developers can use our Unico-GUI to configure the pressure sensor, take measurements, and enjoy a graphical interface to simplify their workflow. Drivers for the LPS22DF are available on GitHub, and a ready-to-use library capable of detecting altitude changes and distinguishing between various vertical movements, such as stairs, elevators, and escalators, is available in the X-CUBE-MEMS1 software package. Consequently, it’s easy to start running simple applications taking advantage of the LPS22DF very quickly and testing the results to start working on an application.