Our MDmesh family of superjunction MOSFETs is celebrating its 20th anniversary and we wanted to look back at the journey that led us to the various series of components that are now so popular in high-voltage systems, but also look at the future of this groundbreaking structure. Twenty years ago, high-voltage applications hit a wall with classical N-Channel planar transistors. They remain one of the most common power devices and use a classic structure with a metal gate that sits above an N- channel that we typically call the drift region or epitaxial layer. The source and the drain, on the other hand, rest on a N+ region that sits on a P+ body. Applying a positive voltage at the gate will repulse electron holes present in the N- channel, allowing the current to flow between the source and the drain.
The problem is that in high-voltage applications, between 500 V to 800 V, the epitaxial layer in a planar transistor exhibits very high levels of resistance, thus significantly limiting on-state resistance improvements. Scholars acknowledge1 that ST was one of the first companies, with Siemens, now Infineon, to use the principle of superjunction commercially to circumvent this issue. Our MDmesh series is so effective, thanks to an on-resistance (RDS(on)) that can go as low as 15 mΩ, that we continue to increase the reach of our power devices. MDmesh M6, rated from 600V to 700V, is the latest development devoted to soft switching topologies with some version maximizing efficiency (DM6) thanks to fast built-in diodes, while our MDmesh K5 pushes the voltage range to 1,700 V.
What are superjunction MOSFETs?
A large part of MDmesh’s success comes from the superjunction principle. Instead of the traditional P+ body present in planar MOSFETs, superjunction devices use P+ columns that dig into the N- epitaxial layer, thinning it out. As a result, the drift region is more densely doped, lowering its RDS(on) by a factor of 4 in some cases.
In our Application Note 1316, we show that at 500 V, MDmesh vastly reduces power losses, which in turn leads to a reduction of the power consumption by 28 % as well as a lower operating junction temperature and smaller packages. Even when a planar MOSFET offers a similar RDS(on), conduction losses are so much smaller on superjunction devices that MDmesh increases power savings by about 13 %. As we reflect on 20 years of innovation, it is essential to understand how we got there to foresee where MDmesh is heading.
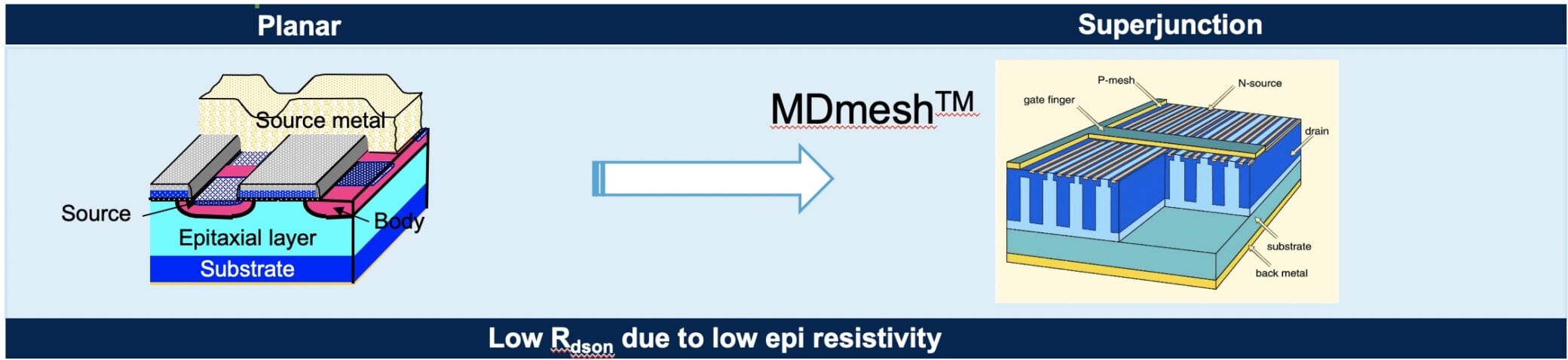
MDmesh: What Happened Before 2000?
In 1978, two Japanese professors at the Osaka University, Shozo Shirota and Shigeo Kaneda, came up with the idea of stacking P and N layers in a varactor (variable capacitance) diode. This led to the first patents in the early 80s that explored the concept of superjunctions with a P-channel that would traverse the layers of P and N semiconductor materials envisioned by Shirota and Kaneda. However, these devices were far from commercially viable, and the industry had to wait for the late 1990s to see ST and its competitor come up with a vertical structure that dug P-columns into the drift region thanks to manufacturing breakthroughs. Indeed, from the time of their conception to the first production samples, ST’s superjunction MOSFETs took less than a year, making them one of the quickest projects in the company’s history.
MDmesh: What Happened After 2000?
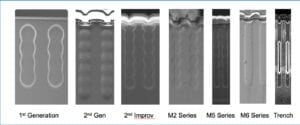
The first MDmesh device officially launched in 1999 and since then, our teams have worked on optimizing superjunctions to make them thinner. The length of the column stayed the same throughout each generation, at 409 µm, but their width went from 11 µm to 5 µm, which significantly improved electrical characteristics, but increased manufacturing complexities. For instance, the first generations of MDmesh devices required between four-to-six epitaxial layers whereas the newest models demand between six-to-12. The thinner they are, the harder it is to align the instruments that will dig into the MOSFET’s body to obtain a viable column. Beyond merely improving specifications, ST also made technical choices early on that enabled us to be the first to offer superjunction MOSFETs with faster diodes, which became very popular in half- and full-bridge topologies.
What Will Happen After 2020?
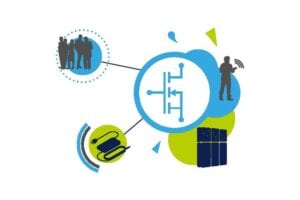
What is even more impressive is that after 20 years, the future of superjunction MOSFETs at ST is bright for two reasons: manufacturing innovations and new applications breakthroughs. When it comes to the technology itself, we are experimenting with deep trench technologies to allow for the creation of the P column in a single step, which in turn would greatly simplify production, shorten cycle time, reduce costs, and make MDmesh accessible to even more customers. New components that use a deep trench approach will also permit ST to enlarge the existing product range, enabling the exploration of new applications. Ultimately, this is highly symbolic because as traditional manufacturing processes start to show their limitations, ST is already exploring new ways to push superjunction devices beyond what the industry thought possible.
The recent advent of Silicon Carbide (SiC) MOSFETs, thanks in part to the electrification of cars, also revealed opportunities for the MDmesh family in applications where customers need the special features and costs of our superjunction devices more than our SiC’s outstanding performances. For instance, medical appliances or electrical relay in planes cry out for MDmesh because they offer a level of stability and ruggedness in the face of critical operation that is not present in SiC devices yet. Similarly, the rollout of 5G base stations represents an excellent boost for MDmesh because our MOSFETs enable the creation of smaller and more efficient supplies capable of handling the massive amount of power inherent to the distributed nature of this cellular network.
- F. Udrea, G. Deboy and T. Fujihira, “Superjunction Power Devices, History, Development, and Future Prospects,” in IEEE Transactions on Electron Devices, vol. 64, no. 3, pp. 713-727, March 2017. doi: 10.1109/TED.2017.2658344 ↩︎