Update, August 1st, 2025
Blue Clover is holding a rooftop event on August 7 at their offices to help companies and engineers in the San Francisco, California, area know more about STM32 assembly lines, the PLT-300A, and their other activities. In honor of this meetup, we updated the article below to talk about their recently released Store-and-Forward feature, which improves the resiliency of the assembly line during Internet outages.
Can a test station on an assembly line be as simple and efficient as pressing a green button? That’s precisely the promise behind the PLT-300A from Blue Clover, a member of the ST Partner Program. The Production Line Tool can flash an STM32 microcontroller, provision the device, launch in-circuit and finished-good testing, and then offer a log to trace the products leaving the manufacturer. It uses a Linux operating system and the PLTcloud to download the firmware before installing it on thousands of MCUs daily and running quality assurance (QA). In a nutshell, it can be a team’s ambassador at the assembly line.
How a global health crisis affected already challenging assembly lines
Testing stations are unique
Testing stations are nothing new. The little QR sticker found on nearly all PCBs tells end users that the system they have in their hands went through QA before leaving the factory. Automating this process is crucial because it helps eliminate human error, increases efficiency, and tracks devices in case there’s a need for a recall or to monitor certain batches. In many cases, the product maker may have to send a representative to the assembly line to set up the testing platform. The reason is simple. Every product is different, so flashing and testing operations are unique. To simplify things, a person familiar with the device must help set things up.
Testing stations are sensitive
Another reason a person involved with the creation of a product would go to the assembly line may be to deliver the firmware and safeguard their IP against theft. Manufacturers try very hard to protect their customers, but no system is perfect. Threat actors often target assembly lines to get their hands on a piece of code or steal products to resell the technology they house. One solution is to send a physical person to deliver encrypted firmware and set up a provisioning system to account for all the devices going through the assembly line.
Testing stations needed a new paradigm
When the global pandemic hit the semiconductor industry and travel was no longer possible, assembly lines faced a massive problem. How would they set up the testing protocols if the person with the knowledge needed to do it could not be on the premises? The obvious answer was to try to do it remotely, but the process is complex and can take four to six weeks. On the other hand, governments were pressuring certain assembly lines to manufacture equipment like ventilators to solve the growing public health crisis at hospitals worldwide.
How the PLT-300A can help creators and manufacturers working on STM32 MCUs
Improved efficiency
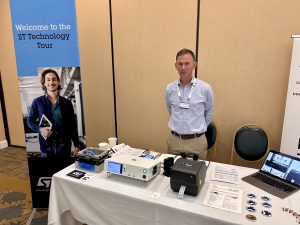
The PLT-300A became the solution for remotely setting up a testing station and solving the challenges created by the global crisis. In a nutshell, manufacturers get a platform where they can connect their finished product, and developers can use it to send their encrypted firmware. Hence, teams benefit from a secure platform and no longer need to physically send someone to the assembly line. Moreover, as Blue Clover explained, instead of needing four to six weeks to set up the test station, developers could do it in half that time. As everything happens on the Production Line Tool, it vastly simplifies the process.
Interestingly, the PLT-300A uses two STM32 microcontrollers, among other devices. An STM32H7 sits on the motherboard with lots of I/Os, while an STM32F3 runs the user interface shown on the screen. Hence, the company has first-hand experience with configuring STM32 microcontrollers. In fact, Blue Clover explained that they can support a new STM32 MCU in a couple of weeks. Once they get ST’s documentation and a development kit, they can create a simple firmware and remotely install it on existing PLT-300As. The Production Line Tool can connect to up to 48 digital test points and 45 analog test points for logic and analog measurements.
Improved security
Blue Clover also emphasized its commitment to security. PLTcloud offers an obvious advantage. The cloud acts as a secure intermediary between the developer and the assembly line. Everything happens within Blue Clover’s environment, including the decryption process, thus protecting IPs from bad actors. Additionally, the company explained that, as a member of the ST Partner Program, it is working with ST to help customers take advantage of features like SFI in STM32CubeProgrammer. In fact, they shared how being an ST Authorized Partner helped them reach companies that needed stronger security protections around their STM32 products because it meant they were working closely with ST.
Hence, Production Line Tools like the PLT-300A highlight a new trend: the rise of a service-based experience at assembly lines. Companies need more than just a testing station. They need a partner that can tailor to their needs and do it in a way that will protect their assets with the latest security mechanisms. And being able to do all this while reducing the need for air travel and offering more testing capabilities positively impacts a company’s environmental footprint. It is becoming easier to ensure greater quality, thus decreasing e-waste and enabling devices to have a longer lifecycle. In a nutshell, even testing stations can help improve sustainability.
Improved reliability
Recently, Blue Clover added a new feature, called “Store-and-Forward”, that preserves the reliability and integrity of an assembly line, even if the Internet goes down. As the video below demonstrates, disconnecting a PLT-300A in the middle of a testing phase has no adverse effect. The production line tool simply continues to store reports onto its 1 TB storage as if nothing happened and will automatically forward them to the PLTcloud whenever it comes back online. The upload is sequential, meaning that it preserves the test order, and the reports are also readable from within the UI if engineers need offline access.