Capacitive MEMS accelerometers now have features and advantages that make them a great alternative to the more expensive piezoelectric sensors, according to a recent white paper from our Alessandra Di Pietro, Giuseppe Rotondo, and Alessandro Faulisi. Entitled Capacitive MEMS accelerometer for condition monitoring, it transforms decades of preconceived ideas and standard practices to show how the industry is evolving to make capacitive Micro Electro Mechanical Systems (MEMS) the new normal in predictive maintenance. As a result, it massively reduces the barrier to entry for many companies that had to previously make substantial investments. Another fundamental benefit of this paper is that it takes a capacitive accelerometer that’s already on the market, the IIS2DH, and it already led to the creation of an evaluation board, the STEVAL-BFA001V1B, which uses the ISM330DLC, meaning that companies can already reproduce its results in their own environments.
As the name suggests, predictive maintenance, or PdM, uses condition monitoring to anticipate when maintenance operations will become critical, and thus plan them when they are the most cost-effective. Traditionally, it allows companies to work on their equipment before it breaks or its performance becomes suboptimal. Hence, predictive maintenance reduces downtime, increases efficiency, and shortens labor-intensive operations that tend to be quite costly. Until now, PdM operations relied on piezoelectric sensors because they were the first to offer the reliability and efficacy necessary for such an application. Indeed, one critical specification is the component’s bandwidth because, for some specific use cases, detecting failure early requires a high frequency. However, today, capacitive accelerometers are reaching bandwidths of up to 5 kHz, allowing them to enter the realm of predictive maintenance.
The Sensors That Are Inside Your Smartphone and Printer
Piezoelectric sensors are one of the earliest and most common devices because piezoelectricity is such a ubiquitous phenomenon. It is characterized by the generation of a voltage by a crystal that undergoes mechanical stress. When resting, a piezoelectric crystal contains positive and negative charges that cancel each other out because of the material’s atomic structure. However, when a force squeezes one side of the crystal, the structural change will generate a positive or negative charge at the opposite end. Hence, it’s easy to understand how a piezoelectric accelerometer can determine movement according to the voltage the crystal generates. There are also many piezoelectric pressure sensors as well as actuators in diesel fuel injectors, printers, or even gramophones, thus showing that piezoelectricity is a tried and true method in industrial or consumer markets.
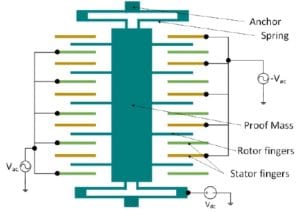
Capacitive sensors may not always be as popular or ubiquitous as their piezoelectric alter egos, but they are at the center of many technological advancements, especially in smartphones and other mobile devices. The technology relies on spring legs trapped between two stationary fingers that act as electrodes and measure electrical potential. Since the spring legs are attached to a proof of mass (or seismic mass) that moves under inertial force, they will get closer to one of the stationary fingers that will measure an increase in capacitance while the other detects a reduction, both enabling the determination of the direction and amplitude of the acceleration. Because capacitive MEMS use a much more complex architecture, they are harder to make.
However, now that their sample rates are much closer to piezoelectric devices in industrial settings, meaning that in a lot of application, such as motors, fans, and pumps, capacitive MEMS offer enough performance and many more advantages.
Capacitive MEMS Are Smaller, More Robust, and Simpler
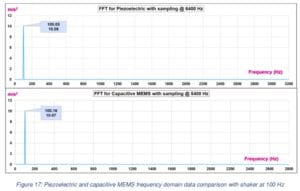
The paper from Alessandra, Giuseppe, and Alessandro is fascinating because it helps readers understand why the industry continues to improve capacitive MEMS instead of just relying on the status quo. Indeed, because of their architecture, they offer a fast recovery time after an extreme shock, and their structure ensures excellent stability over time and temperatures, contrary to a crystal that may be more sensitive to these issues. Sensor nodes using capacitive accelerometers are also easier to design because they do not require an external analog-to-digital converter (ADC) or other signal conditioning circuits, and they can even include a self-test verify the sensor functionality without moving it and regardless of its placement. Overall, they consume less power, they are smaller, and much more cost-effective, thus opening the door to a complete disruption of the predictive maintenance market.
Piezoelectric accelerometers aren’t dead, and they continue to dominate the market when it comes to applications that require devices with extremely high bandwidths, which would be above 10 to 20 kHz. However, thanks to new developments, any system that benefits from accelerometers with 5 kHz sample rates can use capacitive MEMS. In fact, when we compared our IIS2DH device at 5.3 kHz sampling frequency against a piezoelectric sensor at 6.4 kHz sampling frequency, there weren’t discernible differences as the variations were trivial. The results are so close to one another that it is difficult to distinguish them, which means that for the first time in the industry, it is possible to say that relying on capacitive accelerometers for PdM has no downsides on applications that need a bandwidth compatible with capacitive MEMS.
The Sensor Nodes With Capacitive MEMS Are in This Paper
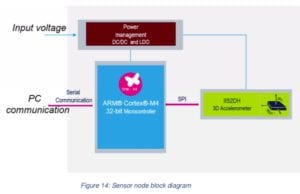
However, we also understand that groundbreaking benchmarks are one thing, but a practical application in the field is another. One doesn’t just drop a more cost-effective but equally performing accelerometer and expect the industry to adopt it overnight. This is why the paper from Alessandra, Giuseppe, and Alessandro is so crucial because it lays the foundation for an entire sensor node. Obviously, they understand that piezoelectric MEMS have a whole ecosystem around them with applications and Graphical User Interfaces to help engineers read their data and benefit from PdM. Hence the elegance behind their paper is that they also show how companies can reproduce an entire ecosystem with an STM32F4 microcontroller and a simple power management module. Just as with a piezoelectric MEMS, a node with the IIS2DH can connect to the USB port of a PC and send all the information necessary to the software.
The results from this research actually led us to release the STEVAL-BFA001V1B, a predictive maintenance kit with sensors and IO-Link capability. The accelerometer on this evaluation board originates from the ISM330DLC six-axis inertial measurement unit (IMU), which is newer and has a higher sampling rate than the model our team used for their paper. Engineers can thus benefit from even better performances. Developers will also have access to demo examples that will show them how they can perform frequency and time domain analysis thanks to the STSW-BFA001V1 software package. Hence, by providing the source codes, libraries, and algorithms, we also greatly simplify and enable the development of PdM applications, therefore increasing, even more, the cost-effectiveness of a sensor node with capacitive MEMS. Hence, this is literally an innovation from our labs to your hands.