On November 12, a day before electronica opens its doors to industry leaders and experts from around the globe, Michael Lütt will give a presentation on Silicon Carbide (SiC), the Enabler of Emission-free Driving. Product Marketing Engineer at ST, he will take advantage of this massive trade event in Munich, Germany to show why we are currently leading the adoption of SiC diodes and MOSFETs in automotive applications, and how this wide bandgap (WBG) semiconductor is transforming our vehicles to bring us closer to the critical adoption of emission-free cars. His talk will also be highly symbolic because it will rest on the work of our many researchers, led in part by Vittorio Giuffrida and Luigi Abbatelli, thus giving the audience a unique look into the innovations and strategies that enabled us to go from the lab to the road.
Indeed, our commitment to Silicon Carbide devices allowed us to offer industry-leading SiC MOSFETs and SiC Diodes for industrial and automotive applications. They both target high-voltage designs thanks to their 650 V or 1200 V rating, depending on the part number, and can tolerate the highest junction temperature on the market today at 200 ºC. However, the road to these industry-changing components was far from simple.
Beyond Cars, The SiC Revolution and Its Impact on Si Devices
Silicon Carbide devices are far from new since a synthetic version in powder form was already in mass production in the early 1890s, and the material found a home in the first radios in the early 20th century. The first LEDs also used a SiC crystal that emitted a yellow glow at the cathode. However, until now the material was much harder to integrate into complex electronic systems because substrates were particularly hard to manufacture, making SiC diodes and MOSFETs too expensive. This all changed when new manufacturing methods enabled the mass production of SiC devices, which are currently transforming numerous industries that rely on high-voltage systems, such as the power converters of Down-Hole-Oil-Drilling machines, data centers’ power supplies, solar inverters, and many more.
However, in preparation for electronica, we sat down with Michael, Vittorio, and Luigi, to better understand SiC in the context of the automobile industry, because it is an excellent example of the extent and impact of the SiC revolution. Indeed, although Silicon Carbide devices increase the battery life of electric vehicles, not many understand that it doesn’t mean the death of more traditional Silicon components. In fact, as much the industry needs SiC diodes and MOSFETs to push electric cars to more driveways, manufacturers still use conventional Silicon ICs extensively for all the vehicle’s digital systems as well as the lower voltage application. Each material has intrinsic properties that offer great value and performance in specific use cases. To grasp the role that Silicon Carbide will play in the future we must delve into its atomic structure and see in what types of designs it will shine the brightest.
Polytypes, The SiC Lattice at the Origin of the Revolution
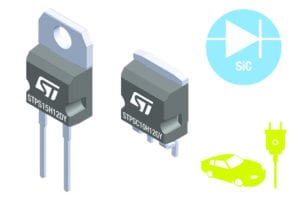
In its most fundamental expression, Silicon Carbide is a compound that comprises Silicon (Si) and Carbon (C) atoms arranged in the shape of a three-dimensional cubic, hexagonal, or rectangular lattice. This atomic construct explains why SiC was so hard to use in an electronic device as its crystalline form massively complicated the industry’s ability to make SiC wafers and build devices on them. Additionally, SiC is polymorphic, meaning that the lattice can take many forms. SiC is actually one of the most polymorphic semiconductors since we currently know more than 250 polytypes, each with specific electrical characteristics.
For instance, the 3C-SiC polytype is made of three bilayers in a cubic lattice (3C). Since its shape offers a higher symmetry, electrons scatter less making it the Silicon Carbide structure with the highest maximum electron low-field mobility at room temperature (1000 cm2/Vs1). On the other hand, 6H-SiC (six bilayers in a hexagonal lattice) may have less interesting electrical properties with an electron mobility of 380 cm2/Vs, but its lesser symmetry makes it much easier to manufacture. 4H-SiC often sits in-between 3C-SiC and 6H-SiC when it comes to a compromise between electrical properties (its electron mobility reaches 947 cm2/Vs) and ease of manufacturing.
SiC, The Wide Bandgap as the Driver of the Revolution
In all cases, the arrangement of Silicon and Carbon atoms in a lattice makes SiC a wide bandgap (WBG) semiconductor because of how the electrons are able to move through the SiC lattice. In the most basic way, atoms contain a nucleus and electrons: 14 for the Silicon atom, and six for Carbon. According to band theory, electrons have two energy states, which we typically represent by two bands. Electrons with high energy are part of the conduction band, and those with low energy are in the valence band. The band in-between is the bandgap, which we characterize in electron volt or eV. The other name for the bandgap is the forbidden gap because electrons cannot exist in it, meaning that they are either in the conduction or valence band.
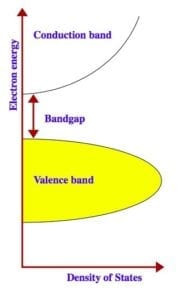
In a conductor, the bandgap is non-existent because the conduction and valence bands overlap. Hence, when we apply a current to a conductor, electrons will flow from the valence to the conduction band and thus let electricity pass through with minimal resistance. On the contrary, an insulator has a forbidden band of more than 9 eV, meaning that at room temperature electrons won’t jump from the valence to the conduction band, thus preventing electricity from passing through.
Finally, semiconductors also have a band gap, meaning that there is theoretically no conductivity at 0 Kelvin, but the forbidden band is small enough that electrons can still move from the valence to the conduction band at room temperature, as long as there’s enough energy pushing them to the latter. Silicon semiconductors have a bandgap between 1 eV and 1.5 eV whereas SiC fluctuates between 2.3 eV and 3.3 eV, depending on the polytype, thus earning the name of wide bandgap semiconductor.
Literally Cooler, The Advantageous Properties of WBG Semiconductors
As Vittorio and Luigi explained:
“Doubling or tripling the bandgap in comparison to silicon means that SiC devices can tolerate much higher voltages and electric fields because the electrons need three times more energy to reach the conduction band. As a result, the breakdown voltage in SiC components is much higher while their on-resistance is far lower.”
Breakdown voltage is the maximum voltage after which an insulator becomes a conductor. According to our research, for a silicon device with a breakdown voltage of 1 V, a similar 6H-SiC model would require 56 V or 46 V for a 4H-SiC component. When developing a high voltage application, such as those relying on the battery of an electric vehicle, the low breakdown voltage of Si devices is undesirable. Additionally, SiC has such a low resistance at 1,200 V that to achieve similar performances a Silicon die would need to be 20 times larger, which means that at high voltages, SiC drastically reduces switching losses, which in turn massively diminishes power losses.
Hence, SiC not only generates lower temperatures under the same high-voltage conditions, but our SiC devices can tolerate a junction temperature of up to 200 ºC whereas similar Si components hover around 150 ºC. Moreover, according to our data, at a switching frequency of 25 kHz, a SiC MOSFET in a 5 kW boost converter would incur a total power loss of 11.1 W versus 25.6 W for a Silicon insulated-gate bipolar transistor (IGBT), and the gap rapidly increases above 25 kHz.
Traction Inverter, The Transformative Applications of WBG Semiconductors
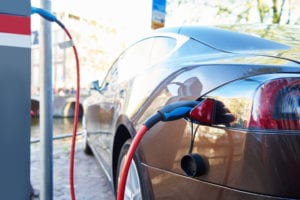
Using WBG semiconductors in a high-voltage design means that engineers can now offer faster switching performances and higher power efficiency, which translates into smaller and easier-to-cool modules. It’s also noteworthy that when dealing with lower voltage rails, traditional Silicon devices still have great performances and their ubiquity means that they will remain at the center of the 12 V and 48 V systems present in our vehicles. However, when it comes to 400 V, 800 V, or 1,200 V, the inherent properties of SiC open the door to new possibilities. Hence, to put the advantages of Silicon Carbide into perspective, Michael’s presentation will focus on a popular example: the traction inverter.
In an electric vehicle, the traction inverter takes a high voltage (typically between 400 V and 800 V) from the battery and produces the three AC phases for the electric motor that will drive the car. At its core, it greatly benefits from SiC devices as Michael detailed:
“SiC enables a reduction in the overall size of the traction inverter because beyond the fact that MOSFETs devices are smaller, they also integrate a very fast freewheeling diode, whereas a bigger Silicon IGBT would require an external one on the PCB. Overall, SiC allows a reduction in size of the traction inverter of about 70 %, which has a snowball effect. Indeed, since the power semiconductor can get up to 80 % smaller, the cooling system and the passive components can also decrease by that much.”
The inherent properties of Silicon Carbide grant engineers the ability to enter new territories thanks to the new levels of performance and efficiency.
Super Charging Cars, The SiC Revolution of Tomorrow That Is Visible Today
SiC also reduced the size of the onboard charger and battery management solution of electric vehicles, which recently led to their integration onto the DC-DC converter and power distribution unit. This remarkable four-in-one solution is already inside commercial battery-powered electric vehicles today and will ensure the proliferation of affordable electric cars. Hence, if the research from Vittorio Giuffrida and Luigi Abbatelli, or the presentation from Michael Lütt teaches one thing, it’s that Silicon Carbide is already transforming the industry and bringing emission-free vehicles closer to the average consumer. Hence, when we say that our SiC MOSFETs and SiC Diodes are changing the industry, it’s because our mastery of wide bandgap semiconductors has already led to real transformations that manufacturers and drivers can already enjoy.
- Comparison of 3C–SiC, 6H–SiC and 4H–SiC MESFETs performances. C. Codreanu, M. Avram, E. Carbunescu, E. Iliescu. Materials Science in Semiconductor Processing. Volume 3, Issue 12, 2000-03-01, Pages 137 – 142, ISSN 13698001, ↩