Even in large and powerful structures, the smallest changes can make a world of a difference, which is why ST launched new Schottky and ultrafast diodes for general, industrial, and automobile applications in SOD123Flat and SOD128Flat packages. Ignoring even the smallest details is a fatal mistake that can cause massive failures or render a design unusable. Similarly, a change of packaging still has tremendous repercussions, especially when a component appears numerous times throughout a board and designers are continually aiming to build smaller PCBs to save costs and improve reliability. Additionally, automakers must also achieve the lightest designs possible to optimize a vehicle’s performance or safety features, which requires the constant improvement of every single component present on the PCB.
Schottky diode | 40 V | 60 V | 100 V |
---|---|---|---|
SOD123Flat 1 A | STPS1L40ZF | STPS1L60ZF | N/A |
SOD123Flat 2 A | N/A | STPS2H100ZF | |
SOD128Flat 3 A | N/A | STPS360AF | STPS3H100AF |
SOD128Flat 5 A | N/A | STPS5H100AF | |
SOD123Flat Auto-grade 1 A | STPS1L40ZFY | STPS1L60ZFY | N/A |
SOD123Flat Auto-grade 2 A | STPS2L40ZFY | STPS2L60ZFY | STPS2H100ZFY |
SOD128Flat Auto-grade 3 A | N/A | STPS360AFY | STPS3H100AFY |
SOD128Flat Auto-grade 5 A | N/A | STPS5H100AFY |
Ultrafast Diode | 200 V |
---|---|
SOD123Flat 1 A | STTH1R02ZF |
SOD123Flat Auto-grade 1 A | STTH1R02ZFY |
SOD128Flat Auto-grade 2 A | STTH2R02AFY |
SOD128Flat Auto-grade 3 A | STTH3R02AFY |
As the table above shows, the new family of diodes covers a wide range of applications. The SOD123Flat devices go up to 2 A, while the SOD128Flat go up to 5 A and are all certified for the automotive industry. It is common to find both of them in LED lighting systems, mobile applications, motor drivers, reverse battery protection circuits, or small power converters. Furthermore, all the general industrial components share the exact same die since the auto-grade versions simply go through a different certification process. As a result, engineers have the added confidence that our Schottky and Ultrafast diodes can still function in very harsh environments and have a long lifespan.
Reason 1: More Performance in Smaller Packages
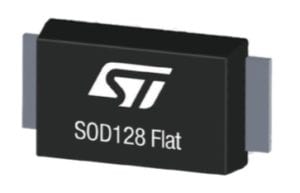
Indeed, the first and most apparent benefit of the new SOD123Flat and SOD128Flat packages is their thickness of only one millimeter, whereas the SMA and SMB packages of the previous generations of rectifiers were twice that size. This is possible because the new structure no longer has U-shaped leads folding underneath the device’s body. As the name suggests, the new components sit flat on the board. ST was able to transition to the new structure without compromising the performance of the diode itself, thanks to new assembly techniques that enable the use of the same die.
Identical silicon in smaller packages also implies a higher power density. For instance, engineers had to previously use SMB packages to obtain a 5 A device whereas the new SOD128Flat packages offer the same current rating in a footprint that’s closer to an SMA package. Similarly, the SOD123Flat package represents a significant reduction in width if we compare it to similar devices that had to use SMA packages until now.
Reason 2: Impressive Dissipation
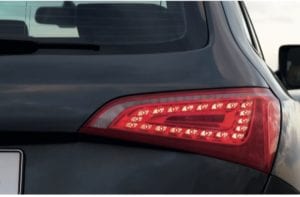
Despite the change in packaging, the diode can still qualify for the AEC-Q101 certification. In a nutshell, the Automotive Electronics Council (AEC) demands that components pass specific stress tests between –40 ºC and +125 ºC to ensure their robustness and to guarantee their reliability regardless of the environments that the car will go through during its lifetime. In fact, our new devices go beyond these norms since they all officially can perform at up to 175 ºC. On a side note, our automotive-grade devices also have a highly dedicated level of traceability, which ensures a manufacturer can track a rectifier all the way down to its wafer. Hence, customers have ultimate assurances, and we are proud to say that their feedback remains consistently positive.
The reason our devices can tolerate such high temperatures in smaller packages is that we use specific clip-assembly techniques to properly evacuate heat. Indeed, smaller surfaces tend to get hot quicker as there’s less room for dissipating the heat a die generates. In the case of the SOD123Flat and SOD128Flat packages, heat travels from the top of the device to the bottom where it is expelled. As a result, ST uses a clip in these new packages because it dramatically improves heat dissipation. Indeed, whereas other companies may use common wire bonds in aluminum, we use copper clips that cover a greater surface on top of the die and therefore provide better thermal conductivity.
Reason 3: It’s the Future
Using SOD123Flat and SOD128Flat packages also increase reliability and improve manufacturing processes. As alignment of the components on the PCB is crucial to ensure that the leads touch the board’s connectors, it is increasingly common to apply a solder paste and use reflow, since a package can better position itself slightly (self-alignment) during that process. At high reflow temperature, the components and circuits don’t suffer, but the solder paste melts, which also has the added property to self-position the part onto the board footprint. The board then goes through a rapid change in temperature to cool the joints and to ensure a stable solder between the diode’s leads and the board’s connectors. The flat design of the new packages helps keep the solder paste away from the bottom of the package, therefore increasing reliability.
Furthermore, SOD123Flat and SOD128Flat packages are more cost-effective, and since their footprint is smaller, manufacturers can produce smaller and thinner devices, further decreasing the bill of material. As we can see, a simple package change has tremendous ripple effects on a company’s entire operation and treating any part of a board as a commodity or afterthought can quickly turn into a nightmare or a missed opportunity for manufacturers, engineers, and the final users.