A team of students from the Sacramento State University, called the Hornet Hyperloop, is developing a pod that will compete in the SpaceX Hyperloop Competition in the summer of 2019. The sub-scale model shows how a self-propelling vehicle could potentially travel in a vacuum tube at an extremely high speed, thus completely changing what we know about transporting people and goods across the globe. Such a project is part of our initiatives to bring ST Technologies in Universities, and it is quite unique because it has a lot of inherent challenges, from safety, aerodynamics, electronics, controls, and power management, among others. We are thus thrilled to be a part of this massive endeavor by offering our NUCLEO-F746ZG board and our X-NUCLEO-IKS01A1 expansion board to the Hornet Hyperloop team as they come up with innovative technologies to potentially transform the way we cross continents.
In 2019, the Hyperloop Pod Competition will celebrate its fourth year. Its objective remains to foster innovation in transportation by enabling students to come up with a pod design that can propel itself and travel about 0.6 miles (one kilometer) in a vacuum tube that has an outer diameter of about six feet (1.8 meters). The judges look primarily at the maximum speed the vehicle is able to obtain while being capable of decelerating safely to avoid crashing into the structure. Additionally, teams must also develop their on-pod communication system to ensure that a vehicle can send information outside the tube about its speed, its integrity, and other critical data. And we are proud that the Hornet Hyperloop team chose our development boards to design a control system that relies primarily on our sensors and our STM32F7 microcontrollers (MCU).
Why Are Two STM32F7s Better Than One?
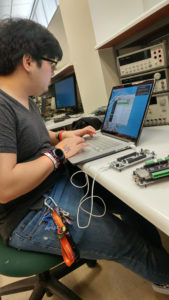
The primary function of the control system is to process the sensors’ data to determine where the pod is in the tube and how fast it is going, which will enable the application to decide what to do next, such as increasing the pod’s speed or initiating the deceleration sequence. The control unit actually uses two STM32F7 MCU for redundancy purposes. The team from Sacramento State University first uses a checking mechanism to ensure that both output the same results, which serves as a way to check the integrity of the overall application. The other reason is that if one of the MCUs fails, the other can take over. Indeed, safety and security are so paramount that it is crucial to have a backup in the event of a malfunction.
However, such redundancy can increase the complexity and cost of a design, which is why the Hornet Hyperloop team heavily relied on the ease-of-use and cost-effectiveness of our NUCLEO-F746ZG development boards. Moreover, the students explained:
“One of the major features that drew us to the ST platform was its power-to-performance ratio. To reach maximum speed, we have to limit the pod’s weight, which means using as little batteries as possible. Hence, finding a microcontroller that’s powerful enough to offer the computational throughput that we need to run our application while still allowing us to reduce our power consumption is the key to success.”
The power consumption considerations are even more significant in a design that requires the use of two identical MCUs because it means that energy savings will literally add up.
Why Are the ST Components Inside the Hornet Hyperloop More Flexible and Reliable?
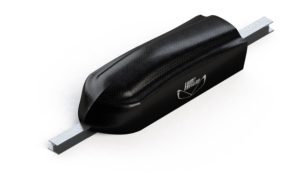
Another reason behind the use of our sensors and Nucleo development board by the Hornet Hyperloop team is the inherent possibilities of our platform to scale with the students’ needs. As they prototype, they need to make their design more powerful or more energy efficient to test different approaches and applications. Since we offer tools to easily configure a microcontroller’s feature-set, it is easy to simulate the performance or behavior of another STM32 to measure its impact on the pod. For instance, STM32CubeMX offers a graphical user interface to help developers configure an MCU with less memory or with a more conservative clock tree to judge its impact on the overall control unit. Additionally, since the STM32F7s are pin-to-pin compatible, the students can swap one for the other without the need to rewrite a lot of code, which makes their design highly flexible.
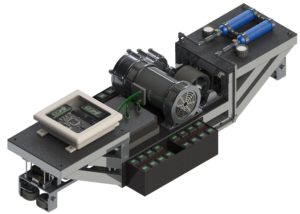
Finally, Hornet Hyperloop also decided to stick with our products after doing vacuum testing at more than 200 miles per hour (more than 320 km/h). Indeed, it may not always be obvious, but the pod undergoes tremendous stress that only the most reliable components can tolerate. A more vulnerable sensor or MCU could output wrong information that could have catastrophic effects. It is thus easy to understand why the students continue to spend time with our products and tools as they prepare for next year’s competition. Additionally, by using reliable components, they can spend more time focusing on other parts of the pod, such as the cooling system for the battery, or the aerodynamic performances of the chassis. We thus can’t wait to see what the Hornet Hyperloop team will bring to the competition, and we are proud to support such an ambitious project.
Check out ST Technologies in Universities:
- The STM32 Step-by-Step Guide Will Make an Expert ST Developer Out of You
- Automated Irrigation System, Smart Agriculture with Nucleo Boards and Sigfox
- SensorTile Capstone Projects Bring Basketball to Machine Learning
- Programming Your STM32 Embedded System in… Assembly?!
- Two Life Lessons from Learning Embedded Systems with SensorTile