On June 11, ST will hold a webinar on STPOWER devices in the context of high-voltage solutions for on-board chargers (OBC) and DC-DC converters in electric vehicles. However, instead of a traditional presentation on the technologies at play, the talk will help engineers figure out the practical applications of Silicon and Silicon Carbide MOSFETs by taking a deep dive into topologies while also looking at benchmarks and why SiC enables bidirectional DC-DC converters. Anselmo Gianluca Liberti, Senior Application Development Engineer at ST, and Luigi Abbatelli, a member of our Power Transistor Division, will lead the webinar and look at various use cases to ensure attendees gain a practical knowledge that will enable them to understand better what is driving the innovations behind today’s electric cars.
We recently saw that New Energy Vehicles are now booming, partly because they are getting easier to manufacture. We’ve been tracking this phenomenon for a while. Two years ago, we were already talking about the impact of Silicon Carbide in cars and anticipating their presence in mainstream models. Today, they are becoming the norm in all sorts of electric vehicles. Traditionally, the industry segregates cars according to their electrification. Mild hybrid electric vehicles (MHEV) have a traditional combustion engine with a generator in parallel that takes over when the vehicle is idle, coasting, or braking. Hybrid electric vehicles (HEV) are now quite common and use a traction inverter to drive the car until the combustion engine takes over. Plug-in hybrids (PHEV) are similar but use an on-board charger, while battery electric vehicles (BEV) do away with the combustion engine altogether.
STPOWER: The Challenges of Efficiency and the Answers From ST
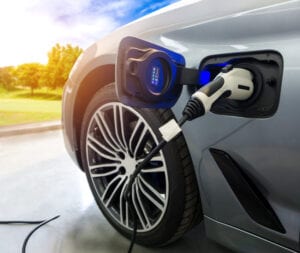
Anselmo and Luigi will invite us to look at electric cars differently by focusing on the EV on-board chargers inside The car’s electrification. Since the presentation focuses on OBCs and DC-DC converters, it makes more sense to delve into charging capabilities because this technical aspect defines the type of power devices that must integrate the system. After all, consumers are now benefitting from chargers that can output 400 V to 800 V to refill batteries as quickly as possible. However, if the OBC or DC-DC converter isn’t efficient enough, consumers lose the gains brought on by new charging technologies. Car manufacturers must also make these modules smaller and lighter, which explains why wide bandgap semiconductors, like Silicon Carbide MOSFETs, are so important. Indeed, in some cases, SiC enables greater efficiency while keeping designs small and costs down to ensure electric vehicles become more mainstream.
The webinar is also a great place to learn about the components that can help answer these challenges. For instance, we have STPOWER MOSFETs MDmesh with a breakdown voltage ranging from 600 V to 650 V, which offers lower switching losses, and our STPOWER SiC MOSFETs that offer faster switching frequencies and enable smaller designs. It will thus be interesting to hear Anselmo and Luigi talk about the various architectures and topologies present in electric cars and how STPOWER devices each have a specific purpose. For instance, the MDmesh DM2 or MDmesh DM6 offer an integrated fast body diode that makes them very attractive in PS and LLC Full-Bridge DC-DC converters. On the other hand, in a bridgeless power factor correction module, using a 650 V SiC MOSFET can be the key to a significantly smaller and more efficient design.
STPOWER: A Change in Package Can Make a World of a Difference
Thanks to rare benchmarks, the webinar will also compare a D2PAK packaging against an H2PAK and a HU3PAK to show, with the help of benchmarks, the importance of the enclosure. The results demonstrate that at the same temperature (around 125 ºC) and with the same die (an STB43N65M55), a model with an H2PAK can reach 1.7 kW while the D2PAK can’t go higher than 1.35 kW. Similarly, when using an STB57N65M5 die at 125 ºC, a HU3PAK can reach 2.2 kW, whereas the D2PAK stops at 1.4 kW. Such a feat is possible because the H2PAK and HU3PAK housings have a Kelvin pin, which vastly reduces switching losses. Additionally, the fact that the heat dissipates out of the top of the device is far more efficient than with the D2PAK, where the heat dissipates at the bottom, which means that the PCB traps part of the heat.
Finally, the webinar will explore the use of a STPOWER ACEPACK SMIT package, which, in our tests, allows a design limited at 2 kW in a D2PAK to reach 3.8 kW. ACEPACK SMIT packages can also house more than one MOSFET or IGBT. In a traditional surface-mount package, the larger die size would constitute a severe problem due to the inability to dissipate heat properly. ACEPACK SMIT housings do not have the same issue, and it is thus possible to put more IPs under one roof. All these benchmarks, and more, serve to teach a valuable lesson: some may think a package has little influence, but the right device can significantly reduce the overall size or enable greater flexibility in the choice of the cooling system. Hence, it’s easy to understand why ACEPACK SMIT packages are so prevalent in on-board chargers.