As the world recently celebrated Earth Day, we wanted to talk about one of our many components that help better manage the electricity people consume every day, and, therefore, decided to focus on the VIPe26K. The high-voltage converter destined for power supplies below 12 W distinguishes itself thanks to a MOSFET with a breakdown voltage (BV) of up to 1,050 V. As a result, the device tolerates a much more extensive range of input voltages than the traditional competing models with 700 V-BV or even 800 V-BV. The VIPer26K is still the only device of its kind that includes a MOSFET with such a high breakdown voltage, making it an excellent device for, among many other applications, smart power meters that typically draw very little power, but must deal with an unusually broad range of input voltages.
The VIPer26K, as the name suggests, is a cousin of the VIPer26, a voltage converter for 12 W power supplies that embarks an 800 V power MOSFET. From a silicon point of view, the VIPer26 MOSFET is based on an MDmesh K3 Power MOSFET technology, and it remains a popular choice thanks to its price-to-performance ratio. However, we noticed that the industry was also asking for a model with a higher breakdown voltage, which explains why the VIPer26K had design wins very early on. The new device draws a lot from its predecessor but is a derivative of an MDmesh K5, which explains its much higher breakdown voltage and its ability to work with three-phase voltage supplies. Let’s thus look at what makes the VIPer26K special.
VIPer26K, No More Stacked FET and an Error Amplifier Embedded
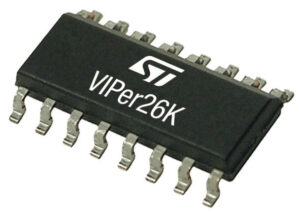
The most apparent benefit of the VIPer26K is the fact that it works as a substitute for a high-voltage plus stacked FET architecture. Traditionally, engineers must stack two MOSFETs with lower breakdown voltage and add passive components to obtain the same electrical capabilities. Additionally, the VIPer26K houses the MOSFET and the controller under one roof. Hence, designers can vastly simplify their PCB, which will lower their bill of materials and improve the overall reliability by eliminating potential points of failure. For instance, when planning for a snubber circuit, which limits the voltage spike due to leakage inductance when a switched-mode power supply turns on, the 1050 V-BV of the VIPer26K means engineers can use fewer components and thus benefit from an overall smaller PCB.
The VIPer26K supports three-phase voltage supplies, which makes it an excellent tool for auxiliary power supplies in industrial settings. The fact that the device also draws less than 30 mW at 230 VAC in standby power means that it will work wonders in a power supply for an LED driver or even a microcontroller, thus largely exceeding the realm of smart meters. The device also comes with a myriad of safety features, from safe auto-restart after a fault condition, to an overcurrent protection and a thermal shutdown system to prevent any damages from overheating. Finally, thanks to the presence of a PWM controller and an error amplifier, it’s easy to include the VIPer26K in many switched-mode power supply topologies, such as isolated flyback (secondary-side and primary-side regulation), non-isolated flyback, buck, and buck-boost.
VIPer26K, Plenty of Development Boards to Satisfy All Topologies
We reflect the flexibility of the device, brought on by the presence of the error amplifier, with the number of development boards that users can choose. The STEVAL-VP26K01B adopts a buck topology, and the STEVAL-VP26K01F is a three output isolated flyback converter whereas the STEVAL-VP26K02F adopts the same topology as the latter but offers a dual output isolated secondary side regulation and the STEVAL-VP26K03F provides a dual output isolated primary side regulation. The last three offer variations for smart meter applications, while the first board acts as a reference design for other more general applications. The STEVAL-VP26K01B is also a cost-effective way to test the safety features of the converter, and the design itself meets the EN55022 – Class B EMI regulation standard with just the use of a simple LC input filter, making it a great starting point for designers.
The STEVAL-VP26K02F is undoubtedly the most common development platform because traditionally, users that aim for an isolated flyback topology will call on secondary side regulation. We also offer the STEVAL-VP26K03F because a primary side regulation means engineers don’t need to use an optocoupler, thus reducing the number of components on the board while still providing isolation. The system loses the precision that comes with a secondary side regulation. However, for many applications, the performance remains- excellent, which makes it a tradeoff that is easily worth it, not only because of costs but because fewer components increase the mean time between failures (MTBF). Engineers looking to get a quick start can find schematics and a bill of material for each board.