The fuel injection Eclipse plugin for the SPC5-Studio IDE recently received updates that enable engineers to rapidly build electronic fuel injection (EFI) applications for engines with as little one cylinder and even use two injectors with one cylinder. Let’s see how teams can build an EFI module with the SPC572L64F2 microcontroller and the L9177A driver.
Lower Emissions Demand Better Electronic Fuel Injection
The first EFI system appeared on the Volkswagen 1600 in 1967 and they continue to rule the automotive industry. According to a 2018 study from J.P. Morgan, as the share of cars with internal combustion engines shrinks to 41% of the global market in 2025, compared to 98% in 2015, hybrid vehicles should also represent 41% while electric cars should account for 18%. Traditional engines are here to stay, which is why regulators continue to expect more efficiency from them. For instance, Euro 6/VI, the latest emission standard from Europe, limits, among many other things, the emission of nitrogen oxide (NOx) by diesel cars to only 80 mg/km, whereas gasoline engines can’t exceed 60 mg/km. Moreover, “17 out of the 20 members [of the G-20] have chosen to follow the European regulatory pathway for vehicle emissions control,” according to the International Council on Clean Transportation.
Electronic fuel injection systems are a great way to meet these standards and vastly increase performances. Injecting fuel into the fuel valve is a necessary process in any combustion engine. However, injecting it at the optimal moment and in optimal quantity is far from easy. In a car, the speed, the load, the altitude, the outside temperature, and whether the driver is starting the engine or using cruise control will significantly affect the time of injection and the amount of fuel. Moreover, EFIs are now increasingly common outside the automotive realm. Consumers are demanding much better performances from their two-wheel vehicles, roadside equipment, lawnmowers, boats, and even combustion engine generators. EFIs are thus a necessity, and building them for small engines can be straightforward thanks to two ST components and our IDE.
SPC572L64F2, a GTM for EFI… OMG!
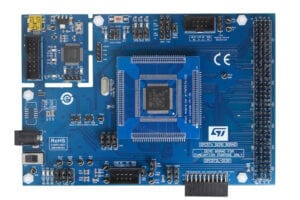
The SPC572L64F2 is an excellent MCU for electronic fuel injection systems because of the presence of a generic timer module (GTM101). This IP can offload the main CPU for several tasks to optimize performance significantly. For instance, it can take the information from the flywheel, thus sensing the position of the engine, and use its hardware unit to increase the signal’s resolution before sending the injection and ignition signals. In our previous generation of MCU for EFI applications, the main core had to process the signal from the flywheel, which took resources away for other computations. Now that the GTM takes care of it, the MCU can use its core for other processes, thus optimizing performances. Developers can also use the GTM to compute the instantaneous speed or run the battery management system by using specific functions.
The SPC572L64F2 is part of our second generation of microcontrollers for automotive powertrain applications, and the smallest device that works in engines with up to four cylinders. It achieves ISO26262 ASIL-A compliance thanks to safety features, such as clock monitoring and watchdogs, to ensure extreme reliability. It also includes a System Memory Protection Unit to guarantee the integrity of the information flowing between the Core and the memory controllers or peripherals. Its single e200z2 core, 64 KB of SRAM, and 1568 KB of Flash make it a particularly exciting component for small engines with one or two cylinders. Developers that want to start experimenting with it can get the SPC572L-DISP, which will enable them to use the MCU’s peripherals, such as CAN, UART, LIN, or FlexRay, and also benefit from two JTAG ports to facilitate debugging and programming operations. The board is fully supported by SPC5-Studio.
L9177A, an Engine Management Module With 2 Channel Injector Drivers
Another critical aspect of any EFI system is engine management. The L9177A is a powerful solution that includes two channels injectors drivers by parallel lines or a serial SPI interface, thus enabling engines with two injectors for one cylinder or two cylinders with one injector each. The injector driver, O2 sensor heater, and the two relay drivers use a Serial Peripheral Interface (SPI) to facilitate developments. Engineers can even start their developments on the EVAL-L9177A evaluation board, which also uses the SPI to read full diagnostic information. Additionally, the board protects all channels against short-circuit, overcurrent, and overheating. Teams that wish to try the EVAL-L9177A plug it onto the connector of the SPC56M-Discovery board, which uses an SPC563M64L7 MCU. However, once developers are familiar with the L9177A and the SPC572L64F2, it’ll be fairly straightforward to switch to a custom design that includes both components.
SPC5-Studio IDE and SPC5-L9177A-K02 Reference Design, Making EFI Systems Accessible
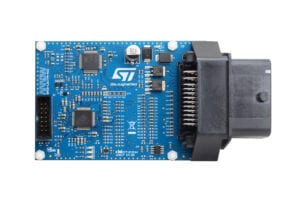
Part of the reason that moving from one SPC5 MCU to another is relatively simple is that we also provide libraries for our SPC5-Studio IDE that greatly facilitate developments. Whether teams are developing an adaptive front lighting solution or an electronic fuel injection system, we have frameworks that greatly assist software engineers. For instance, the IDE includes libraries for the generic timer module of the SPC572L64F2 to more quickly optimize the injection or ignition processes, among many other things. Additionally, teams can also request a demo EFI application from ST to hasten the prototyping phase. It will help them see how we implemented certain features, and it will also act as a configurator to quickly define the number of injectors per cylinder, the flywheel, and, ultimately, get a functional application.
We also worked on a reference design with Arrow, the SPC5-L9177A-K02, which embarks the SPC572L64F2 and the L9177A. The software that comes with it will help create a basic fuel injection control system for one injector and one cylinder, and it already helps meet the Euro 4/IV, Euro 5/V, Bharat Stage VI, China V, and China VI, emission standards. However, the board itself opens users to the full power of its components, which means that it will allow programmers to go beyond the demo application to create applications with up to two cylinders and up to two injectors. It’s thus an excellent solution for engineers that want to focus on EFI applications and are looking to shorten their time to market.
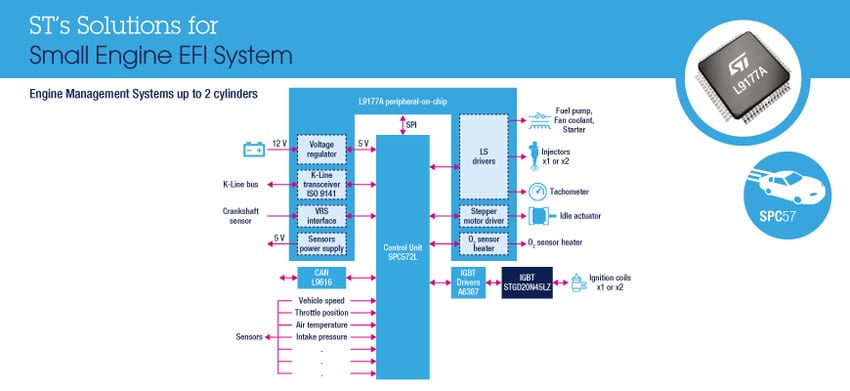