The ST Ang Mo Kio (AMK) TechnoPark in Singapore will receive the country’s largest district cooling system (DCS), with a cooling capacity of up to 36,000 refrigerant tons. Estimated to be operational in 2025, the system will help reduce annual carbon emissions by up to 120,000 tons, or the equivalent of 109,090 fewer cars off the road, thanks to the installation of new PFC abatement machines. Indeed, the cooling infrastructure will enable the removal of existing chillers, which will then open spaces for many environmentally positive initiatives. Hence, the 120,000 tons metric is simply an estimate of the project’s most direct impact but the district cooling system will have far wider ramifications.
ST is working with the SP Group, Singapore’s national grid operator, whose team will build and manage the installation. The project is also SP’s first industrial DCS as the company has only led residential and commercial installations until now. Similarly, the ST AMK TechnoPark is ST’s first facility to benefit from DCS, thus further cementing our commitment to carbon neutrality by 2027.
Why a District Cooling System?
Composition of a District Cooling System
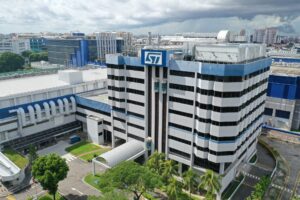
In a DCS, one plant cools water before sending it to a network of underground pipes that serve various buildings. The system thus pools resources to increase efficiency, reduce environmental impacts, and save space. Buildings no longer need chillers, saving power and maintenance costs thanks to the central plant. Moreover, a loop sends the water back to the plant to cool it again. The main plant also stores water. Cooling therefore can happen during off-peak periods to improve the efficiency.
According to the Encyclopedia of Energy1, the first significant DCS project dates back to 1962 and was installed in the United States. The technology garnered some interest in the 70s before subsiding. DCS became popular again in the 90s as regulators mandated chlorofluorocarbons (CFC) reduction. And now, district cooling systems gain new grounds as the world looks to reduce carbon emissions and recycle water. ST is thus surfing on this new wave to meet its sustainability objectives and work with a local partner to advance this promising technology further.
Why the ST Ang Mo Kio TechnoPark?
Anatomy of a Unique Project
The AMK TechnoPark is ST’s largest wafer-production fab by volume. Bringing DCS to that particular site will thus have significant ripple effects. Traditionally, projects of this size target urban developments. For instance, the Deep Lake Water Cooling infrastructure in Toronto, Canada, has a similar capacity (40,000 tons), but the distribution network covers a chunk of the downtown area. The ST and SP Group infrastructure is thus unique because it’s one of the first at such a scale to cool an industrial manufacturing plant. It is also a first in the semiconductor industry. Most projects from competing fabs retrofit new chillers. With this new DCS, ST can re-purpose the space in favor of something much more efficient.
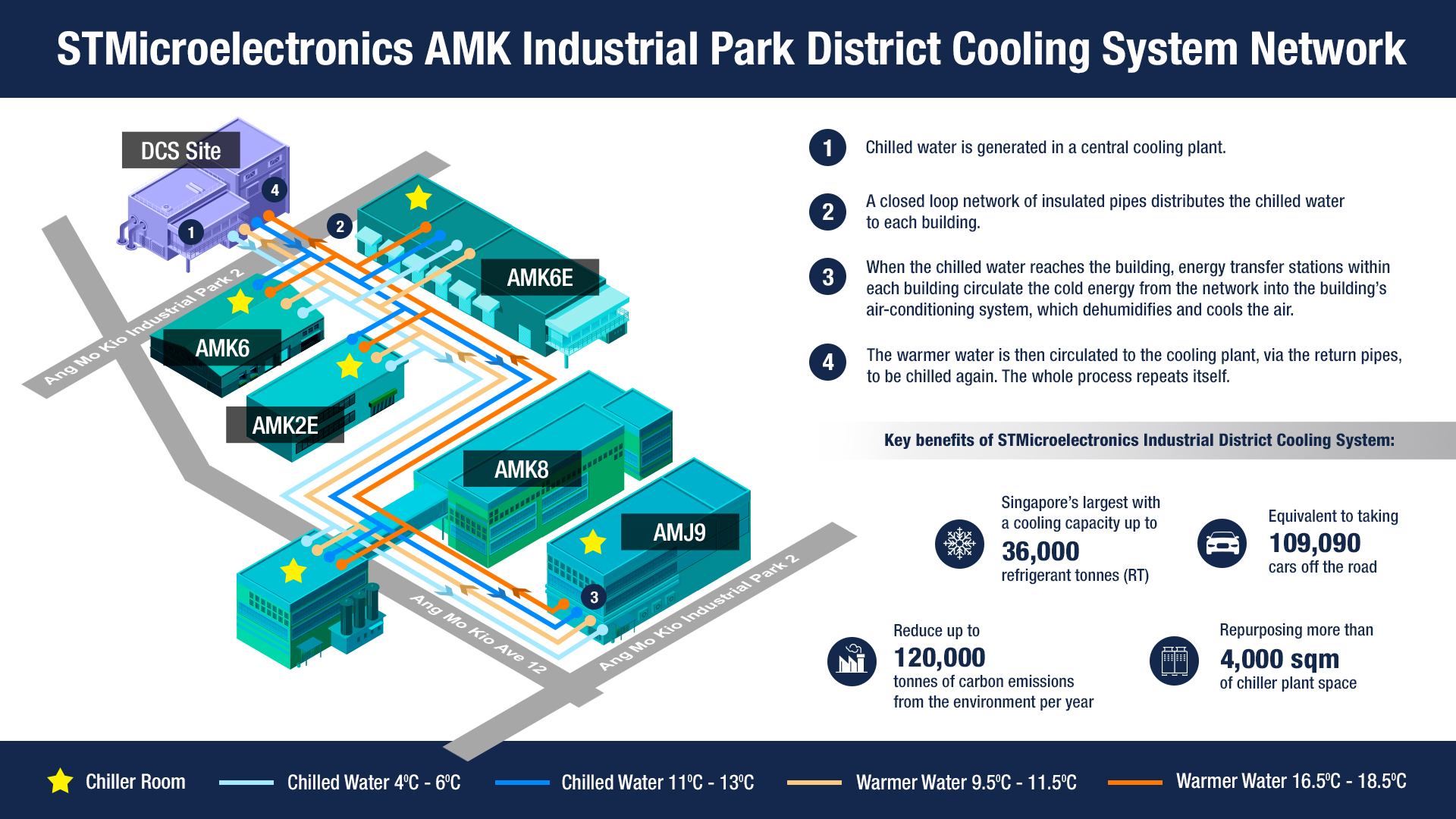
The project will cost an estimated USD 370 million, including the construction of the central cooling plant right next to the TechnoPark. Beyond energy savings, removing chillers within the ST plant will free up space for other environmental programs. For instance, the AMK site is looking at water conservation and solar panels, among other things. The SP Group should start construction of the central plant this year and is committed to managing the project for at least the next 20 years. Singapore also hopes that this project will inspire other companies. As Ms Low Yen Ling, Minister of State, Ministry of Culture, Community and Youth & Ministry of Trade and Industry stated,
“I hope this initiative will inspire many more innovative decarbonization solutions across other industrial developments, and spur more companies to seek opportunities in sustainability.”
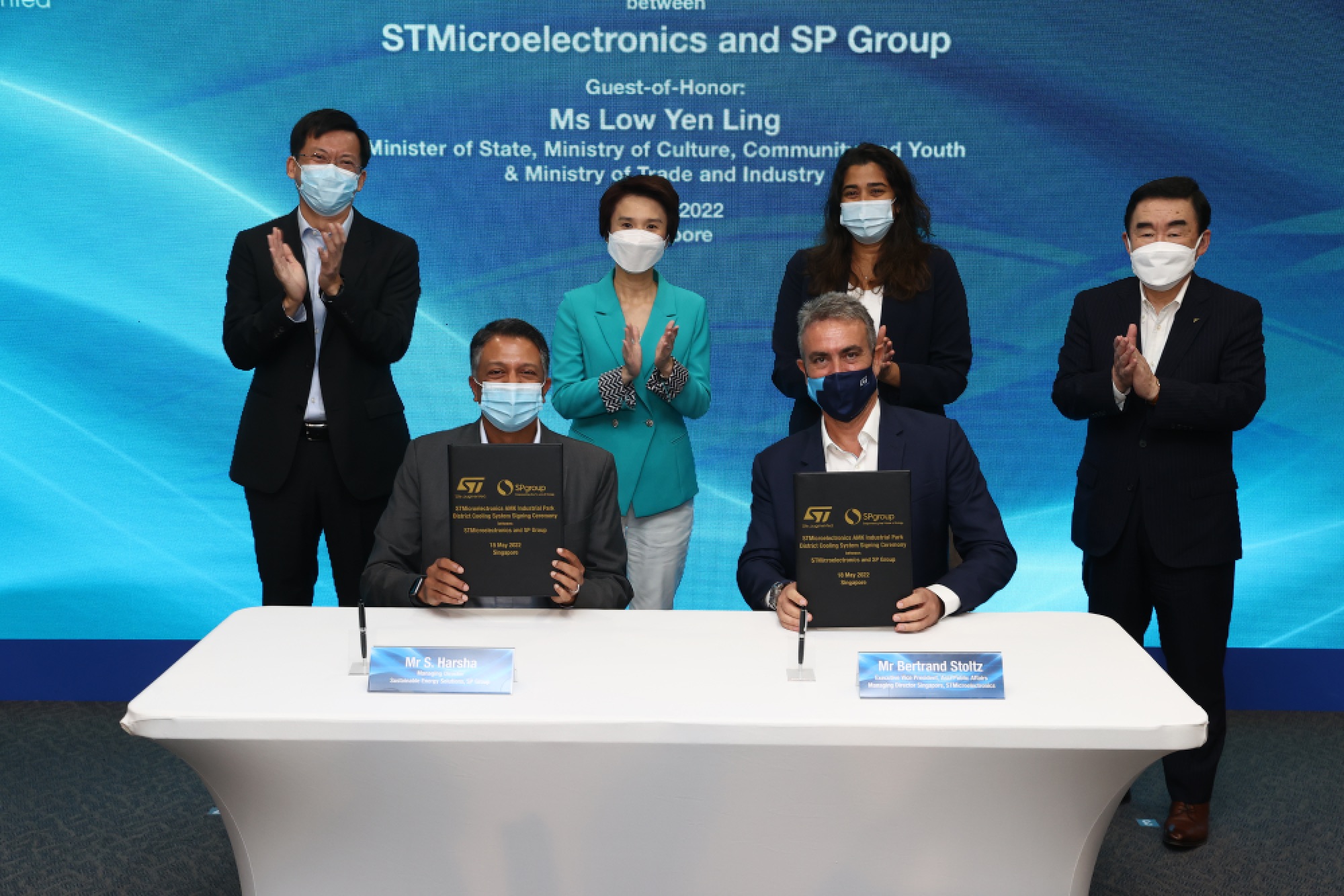
- Sven Werner, “District Heating and Cooling,” in Encyclopedia of Energy,
ed. Cutler J. Cleveland (Elsevier, 2004), 841-848, https://doi.org/10.1016/B0-12-176480-X/00214-X. ↩