Let’s take a step back and look at everything we covered during ST’s first live stream at electronica 2022 on smart mobility. For those who missed it, you can watch the replay on our event platform and see how experts, industry leaders, and partners are finding new solutions to smart mobility challenges. This is also the opportunity to provide links and additional content for those who want to explore the products and concepts addressed during the talk show.
Table of Contents
Smart mobility and battery management systems
When people hear “smart mobility,” they often think of electric cars. While battery-powered vehicles were still rare a few years ago, they should become mainstream worldwide by the decade’s end. However, engineers, and decision-makers must still solve engineering challenges, one of them being the management of the large battery needed to drive those vehicles. As the battery’s capacity increases substantially, it becomes more difficult to monitor it, which can affect its performance, lifespan, and safety.
Demo: ’67 by Charge Cars
ST showcased the ’67, an electric muscle car by Charge Cars and we invite you to check the live stream to see why it is attracting so much attention at the show. The ’67 by Charge Cars has a new steel body shell and a 63 kWh battery offering 200 miles of range and 400 kW of peak power. Thanks to a powerful battery and two powertrains driving four electric motors, one for each wheel, the car can go from 0 to 60 miles per hour (mph) in 3.9 seconds and has 1,520 newton meters of torque. A muscle car today usually goes from 0 to 60 in about four seconds and features 570 newton meters of torque.
The floor-mounted battery of the ’67 rests in a tray that’s a structural part of the body shell. The battery cells are at the heart of the vehicle, both physically and technologically. Consequently, a battery that drains too quickly, charges too slowly, or has a short lifespan will negatively impact the user experience. Manufacturers must add a robust battery management system to create a great driving experience. It’s the reason why Charge Cars partnered with Arrival, a British manufacturer that worked with ST to create the battery management system found inside the ’67.
The car is an absolute labor of love, which means that Charge Cars will limit its production to 499 units and set a starting price below USD400,000.
Demo 2: BMS reference design with L9963E from Arrival
Arrival showcased a reference design for its battery management system on the ST booth. The transparent case lets attendees see the board and the ST components used, such as the L9963E and the SPC58EC. Put simply, Arrival explains that it’s imperative to provide reference designs that manufacturers can implement efficiently. It’s the reason why the Arrival demo is so important. It gives industry leaders a path to a solution that will help them release mainstream vehicles faster while also scaling one reference design to either lighter or heavier modes of transportation to optimize their return on investment. Indeed, Arrival also has BMS designs for buses or vans, among others.
Why did Arrival and Charge Cars choose a BMS with the ST L9963E?
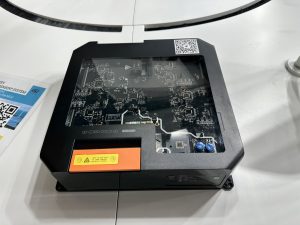
The L9963E includes multiple sensing elements for each of the battery’s cells and one ST L9963E can measure up to 14 cells with 0 desynchronization delay. Put simply, it’s fast and highly accurate, with a maximum error of only ±2 mV.
The redundant sensing elements also mean that the device can crosscheck readings from its analog-to-digital converters to guarantee accuracy. The L9963E also includes other safety features, such as over- and under-voltage protections. ST also provides mechanisms to guard against overheating and overcurrent.
Besides the L9963E, ST has a portfolio of devices for all critical BMS functions, such as the SPC58EC microcontroller, as well as power and safety components, therefore representing a one-stop-shot for Arrival’s key requirements. The electrification of mainstream vehicles demands turnkey solutions that are easier to implement. It’s by saving time, money, and resources that engineers can bring electrification into more cost-effective smart mobility systems.
How did Arrival create its reference design?
Arrival took advantage of the L9963E evaluation board with a microcontroller (EVAL-L9963EE-MCU) to jumpstart its smart mobility initiative. The platform uses an SPC574S64E3, which runs at 140 MHz and includes 6 MB of storage. It allows ST to pre-load firmware that lets developers start experimenting with the design in minutes and quickly write applications. Engineers connect the board to a computer using a USB port and launch the L6693 graphical user (STSW-L9963EE) interface to test parameters or experiment with various features. Furthermore, we also provide a node evaluation board with just the L9963E. The node attaches to the board with the microcontroller and can help engineers daisy chain multiple systems when managing many battery cells simultaneously.
Power distribution systems or the move to digital in smart mobility
If smart mobility is often synonymous with the electrification of vehicles, another vital transformation is the move to digital systems. By moving from analog to digital paradigms, manufacturers can create cheaper and more reliable designs, which is quintessential to the democratization of new modes of transportation. By nature, a digital system provides greater levels of modularity, which helps with scalability. It also helps shrink designs, which increases robustness and reduces costs. Put simply, smart mobility isn’t simply about adding a battery but rethinking energy distribution to make it more intelligent and vastly more efficient.
Demo: Smart fuse box with the VNF1048F
To show attendees what a smart power distribution system looks like when talking about smart mobility, ST presented a demo board featuring STi2Fuse smart switch controllers (VNF1048F). Instead of a traditional fuse box with mechanical elements, the smart fuse offers an astonishingly smaller system. The physical demonstration is thus critical to show OEMs and decision-makers the leap that smart fuses bring. The move also reduces the bill of materials, making the system far more cost-effective, and helps save between 10 kg and 15 kg. The reduction in components also means that the system is more robust as there are fewer points of failure.
Why use the VNF1048F?
The STi2Fuse is a high-side switch controller for 12 V, 24 V, and 48 V applications, which means anything from e-bikes to trucks. Moreover, the device can interface with microcontrollers using 3.3 V or 5 V, which opens it to a wide range of devices. It provides i2-t (pronounced current squared through time) protection to prevent overheating wires due to an overload. While a traditional fuse may let a short surge of current through, the current sensing capabilities of the STi2Fuse will offer faster protection and greater precision. Consequently, it’s also possible to reduce the battery as there are smaller overcurrent spikes, leading to a reduction in size, weight, and costs.
The VNF1048F from ST includes current sensors that report directly to the MCU using an SPI interface. Suppose the ST device detects dangerous conditions and breaks the circuit. In that case, the smart fuse can keep the conditions in memory, so when the microcontroller decides to reactivate the circuit, the smart fuse can rapidly detect if the dangerous conditions are still there. The increased robustness also means that makers can use wires with a smaller diameter since the smart fuse has a much faster and smarter reaction time, thus improving the protection of the PCB traces, connectors, and wire harnesses.
How to get started?
To help teams get started, ST designed an evaluation board with the VNF1048F (EV-VNF1048F). Users place it onto the SPC58 evaluation board (EV-SPC582B) and run the dedicated graphical user interface (STSW-EV-VNF1048F) to start experimenting with ST’s solution. Engineers can also take inspiration from the stack itself to start working on their PCB layout since we provide schematics. Teams can quickly test the VNF1048F and see how it fits into their smart mobility design.
Stellar in the context of smart mobility
The electrification and digitalization of smart mobility imply the increased presence of microcontrollers. OEMs and car makers are integrating systems, which means using one powerful MCU to run multiple applications instead of a myriad of small systems Consequently, applications are increasingly complex and sensitive, leading some to characterize e-bikes or e-cars as computers on wheels. Put simply, the new vehicles shaping the market today are increasingly defined by software to the point that the industry is now calling them “software-defined vehicles.” For this reason, Stellar P and Stellar G microcontrollers are called Stellar Integration MCUs and have features that enable them to run multiple systems simultaneously.
Demo: Virtual machines on Stellar G7
ST is showcasing a Stellar G7 running multiple virtual machines to demonstrate practically the capabilities levied by software-defined vehicles in smart mobility. In a nutshell, a virtual machine takes the hardware resources available and simulates a computer system. They are popular because it’s possible to run multiple virtual machines simultaneously without using various hardware components. The challenge is that running virtual machines requires a hypervisor. A hypervisor takes the physical resources and creates virtual machines to simulate a computing system. Hypervisors are, therefore, very resource intensive.
The Stellar G7 solves this challenge by including hardware IPs that optimize virtualization. Put simply, the microcontroller accelerates functions that hypervisors use, thus enabling the creation of multiple virtual machines without bringing performance to a halt. In this demonstration, ST worked closely with OpenSynergy, a German software company that created a hypervisor called COQOS Hypervisor, optimized for the Stellar family of products. The ST demo shows that manufacturers can now use the virtualization capabilities of the Stellar G7 to run different ASIL levels on the same hardware. The hypervisor isolates all virtual machines, meaning they function independently as if running on dedicated systems. OEMs can thus meet the most stringent requirements using only one hardware platform.
What features must software-defined vehicles have?
To support recent developments in software-driven smart mobility, ST released two categories of Stellar Integration devices: Stellar G, which we featured in the demo, and Stellar P. Stellar G is for zone controllers, gateways, and body integration. Stellar P helps simplify the design of domain-oriented applications like the drivetrain or the vehicle’s body functionalities.
All Stellar devices support over-the-air updates and even include a mechanism that helps reduce memory usage by 50% during an update compared to a traditional OTA implementation. Vehicle makers can patch vulnerabilities or add new product capabilities to create original revenue streams. All of a sudden, smart mobility is more than just the electrification of vehicles but the “appification” of the experience. Users could buy more features over time or port functionalities to a new model by simply transferring a subscription. Similarly, manufacturers may not have to recall a car or e-bike but could release a patch over the air. Software means transcending the physical vehicle and moving to a smart mobility economy.
Communication is another priority in the achievement of smart mobility. Hence, all Stellar devices support CAN-FD, CAN-XL, and LIN interfaces. The Stellar G and Stellar P also have an ethernet controller for high-speed communications. Consequently, Stellar devices can talk to more types of modules and support newer protocols like CAN-XL, which supports a greater payload, and helps future-proof systems. Finally, the Stellar devices meet the highest standards in security and safety.