The KST3420 and KST3220 are distance sensors by KS Technologies (or KST), an authorized member of the ST Partner Program, and a case study in the use of ST’s time-of-flight sensor. The products and engineering services company deployed thousands of distance sensors in various applications and multiple countries over the last four years. For instance, some monitor the trash level across bins in a theme park to optimize garbage collection, while others serve farms or smart cities. Moreover, many engineers will appreciate that the KST3420 and KST3220 took only 45 days to prototype. As most prototyping often takes months, if not years, we sat down with KST to learn from their experience.
Table of Contents
Chapter 1: Challenging Assumptions
Riddle me This – The Trash-Level Question
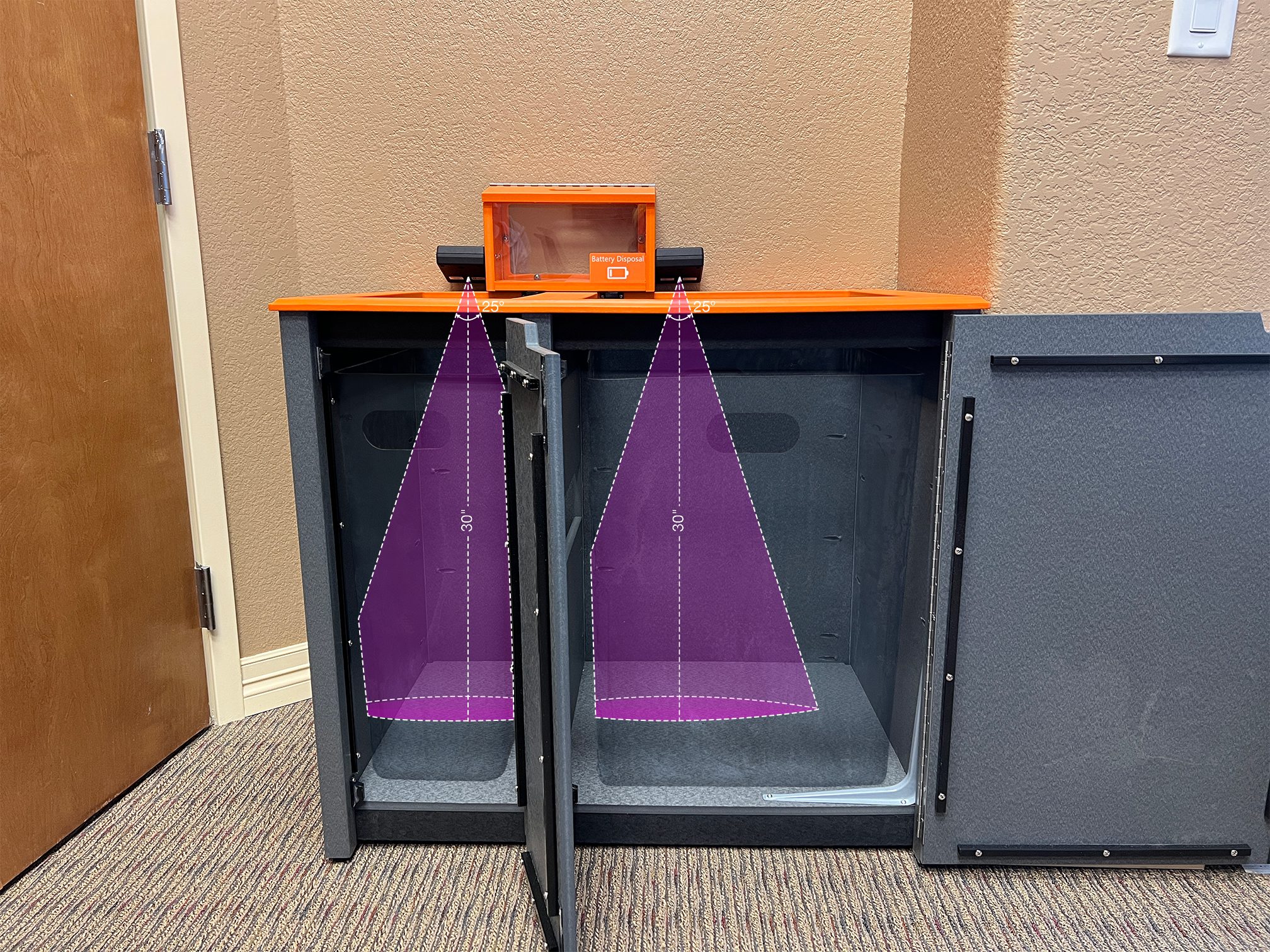
KST’s story started with a question: “what was the best way to measure trash levels in a bin?” As we saw during electronica 2022, the challenge is tricky because the sensor must work under various lighting conditions and bin geometries while providing long battery life. At the beginning of KST’s journey, a few years ago, many weren’t sure what would work best to detect fill levels. The problem was that a particular customer approached KST because their current installation had low accuracy and compromised battery life. Additionally, the client was using Sigfox to link their current sensors to their cloud and would thus require supporting the sub-gigahertz network.
Trial by Combat – Photo Diodes vs. Ultrasonic Arrays
While the problem of measuring garbage can fills posed itself, KST’s engineers were experimenting with the VL53L0X, the smallest time-of-flight sensor at the time. Hence, KST grabbed a Nucleo board and a Nucleo shield with the MEMS to showcase it to the client. However, the customer also requested a prototype with an ultrasonic sensor. A prevalent sentiment was that the latter would be more accurate than a SPAD (Single Photon Avalanche Diode). KST thus ran both products for about two months. Ultimately, the VL53L0X’s superiority was so decisive that the customer didn’t look back.
A Brave New World – 8,000 Sensors in the Field
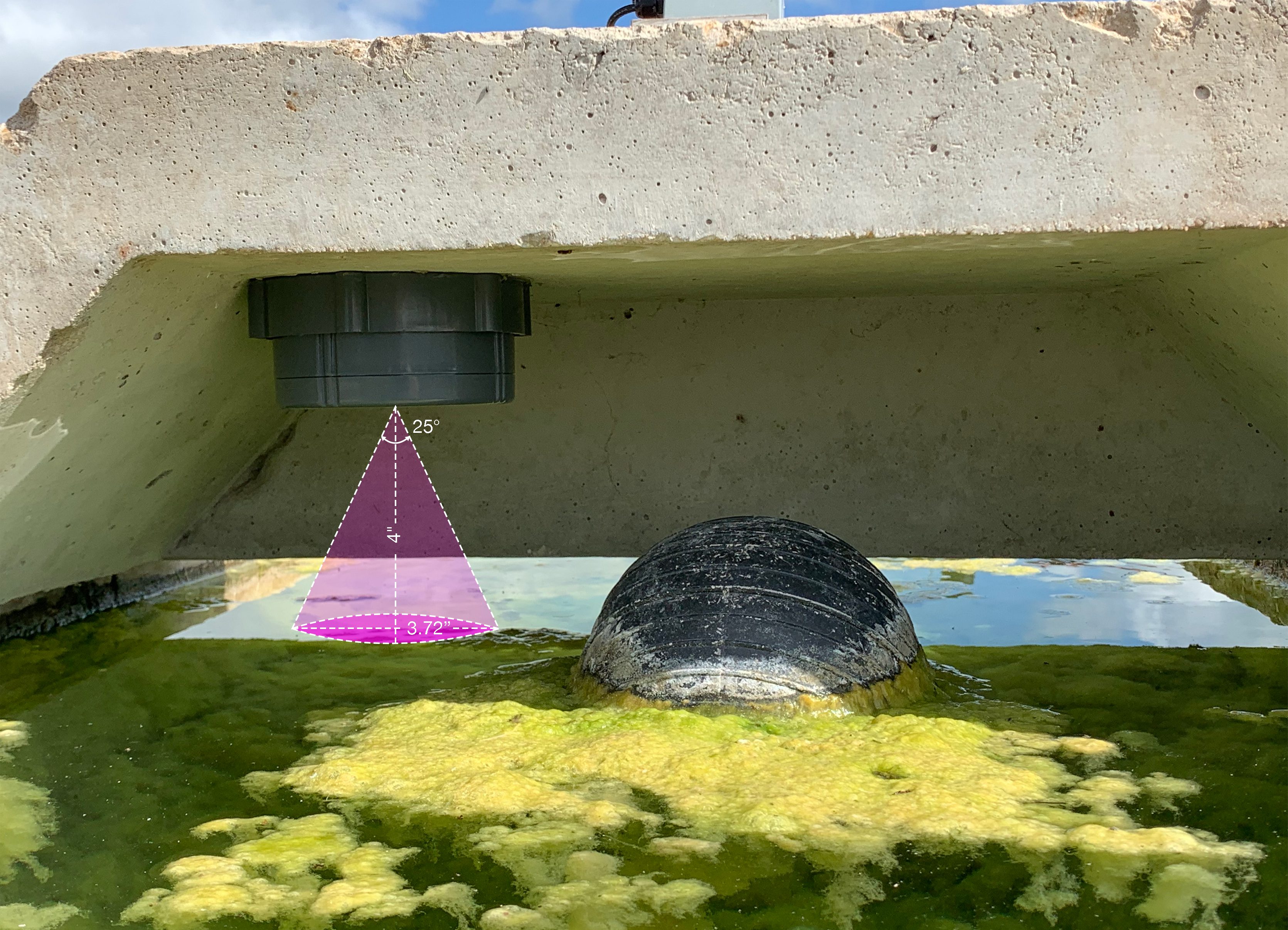
By the end of the showdown, KST had a prototype that would serve as a foundation for its product development. Indeed, not only did it help sit the superiority of the VL53L0X, it showcased the STM32. The client found it meaningful to see that the same MCU on the Nucleo board would end up on the custom design. It was a clear path forward to production, which led to the KST3300, the first generation of KST’s distance sensor. KST deployed it across 8,000 garbage bins and managed the IP. As a result, the ST Partner could bring the distance sensor to other corporations and continue improving on it. On the other side, KST’s client had assurances of maintenance and supply.
Chapter 2: The Rise of Innovations
The Fellowship of Engineering – The New Industry Demands
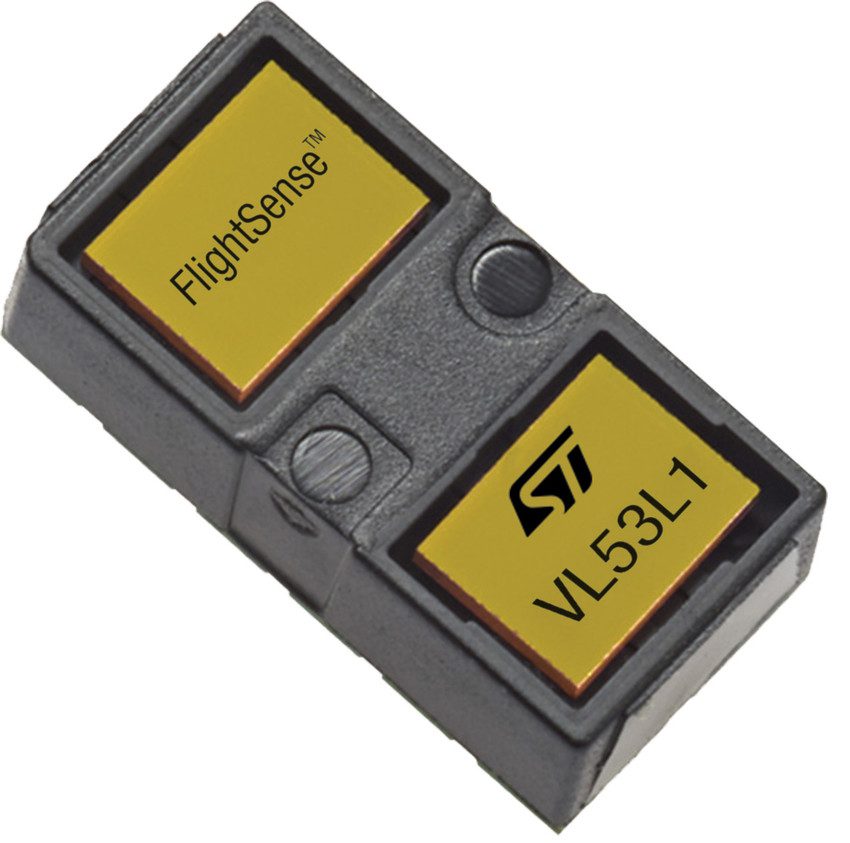
As KST demonstrated its design to more clients and regions, its engineers discovered a broader range of needs. For instance, some wanted a different protocol than Sigfox, with many leaning toward LoRaWAN, Bluetooth Low Energy, and Wi-Fi. Many companies already had a sub-gigahertz network of choice, and KST had to adopt it. Additionally, the design team at KST wrote their drivers for the KST3300. While it helped them ship faster, there were performance issues in direct sunlight or very close range (between 0 mm and 100 mm). Finally, KST wanted to improve its detectors’ battery life to make them even more appealing.
Peeling the Curtain – Adopting LoRa and Sigfox
KST worked on the second generation of its distance detector to meet these challenges. The company moved to a Murata module, which embeds an STM32 microcontroller and Semtech module supporting Sigfox and LoRa modulations. As a result, KST could offer greater flexibility and adapt to nearly all of its customers’ existing infrastructure. Concretely, it meant keeping the customer that had benefitted from the KST3300 while being able to deploy sensors to other applications, such as smart cities.
A Star Is Born – Improvements All Around
To improve performance and battery life, KST grabbed the VL53L1X, which had just come out, and got hold of ST drivers. The new device brought the ability to monitor multiple zones, which opened their detector to new applications, such as people counting. Moving to the ST drivers also enabled new low-power modes, improved calibrations, and reduced crosstalk. Furthermore, KST adopted ST lenses, which, combined with the other measures, ensured greater performance in very short ranges. The new MEMS also fit right into the Nucleo family of products, which hastened prototyping. And that’s how the KST3320 was born inside KST’s lab.
Chapter 3: The Leap in Prototyping
Not in Kansas Anymore – IoT in Harsher Realities
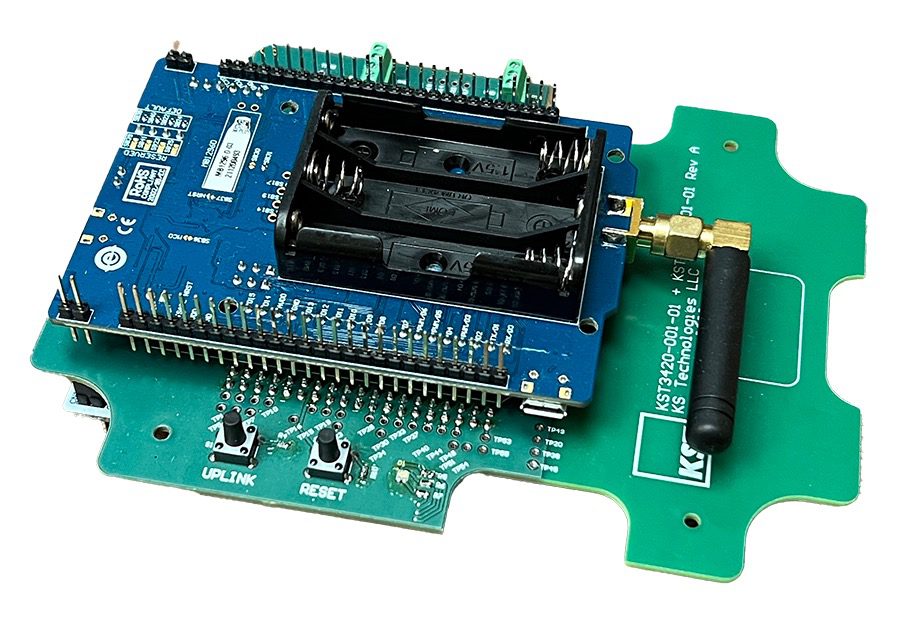
After releasing the KST3320, KS Technologies started receiving a new request: unbundling the RF from the rest of the product. The reason for this demand is that it ensures the system works in more applications. For instance, a client asked to measure water levels under big concrete blocks. In such a setting, putting the RF module outside the trough vastly increases the radio’s efficiency. Moreover, the new demands for KST’s sensors often meant using the product in harsher environments. Whether in the sweltering heat of the American South or the frigid Canadian winter, the sensor had to work in extreme conditions. Finally, KST was looking to improve its product’s battery life.
Divide and Conquer – The Advent of Modularity
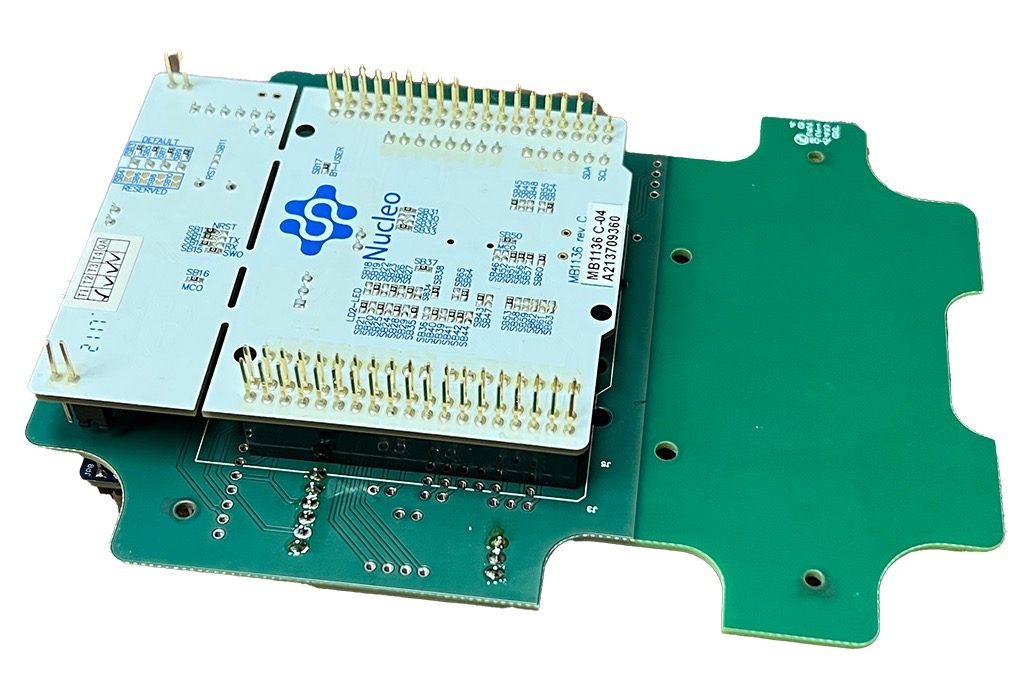
After its first and second generations of products, KST took a different approach and adopted rapid prototyping. The company developed an interposer board that sits between the STM32 Nucleo board and the Murata shield. As a result, KST can now prototype any sensor board using an Arduino connector to break all signals or reset the device. The whole unit sits inside an IP67-rated enclosure and can live separately from the sensor. To connect both, KST uses a threaded connector that’s readily available, which means that it won’t drive costs up. That’s how the company came to use the STM32WL in their KST3320. By adopting rapid prototyping principles, the company moved to a new MCU to meet new wireless demands.
To further promote modularity, KST also came with provisioning and application servers. Their goal is to provide software tools that help take advantage of the sensors. Consequently, KST worked on a cloud-based dashboard and a notification system. Indeed, as the KST3420 and KST3220 came to see the light of day, the company also built an entire infrastructure to push the data from the field to the people that need it to make decisions. Put simply, KST worked on a comprehensive prototype, rather than a basic proof-of-concept.
The Last Frontier – Penetrating New Markets and Regions
The modularity of the KST3420 and KST3220 meant that KST developed versions of its product that included the VL53L3CX , and its teams are already looking at experimenting with the VL53L5CX. Hence, whereas most prototyping operations would take months, if not years, KST prototyped its new generation of products in 45 days. Moving to a modular approach also helped them weatherize their system to support harsher environments. Consequently, the service company deployed the KST3420 on a ranch in Texas and in Calgary.
Epilogue
Great Engineering Teams Ship
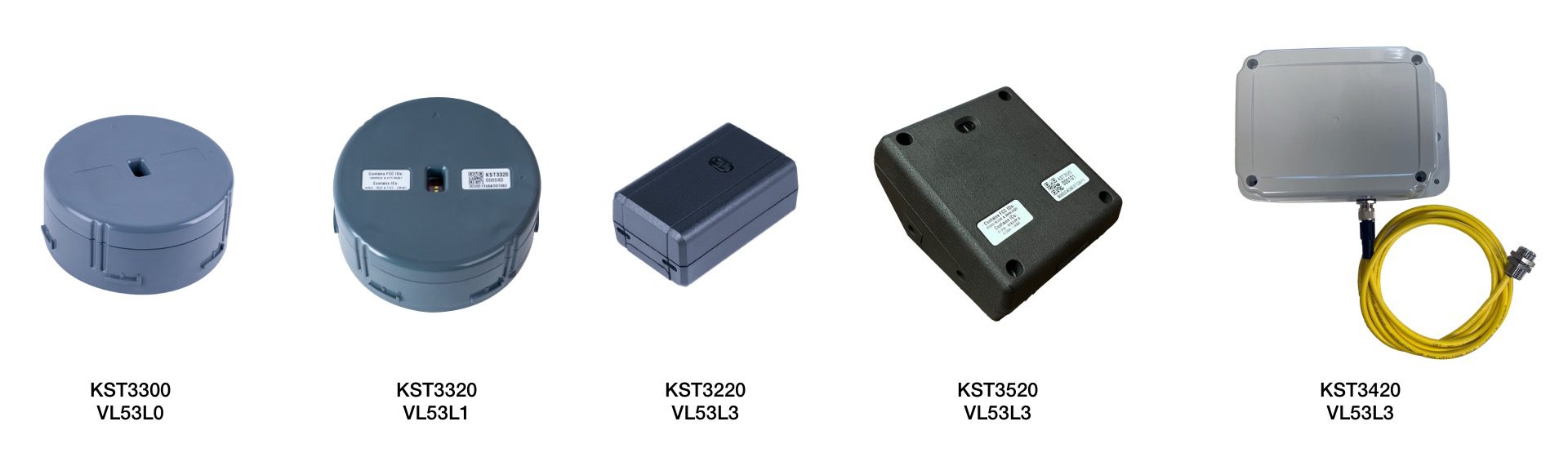
Taking a step back, there are many lessons for engineers and design houses, the first being that it’s essential to ship and learn rather than to wait to know everything before shipping. Because KST identified a novel solution, the client that used the KST3300 saw a return on its investment in just four months. KST was also very honest about the imperfections of its custom drivers or some of the performances of its first generation of products. However, without the KST3300, there is no KST3320, KST3420, or KST3220, which ultimately enabled them to reach a rapid prototyping phase of just 45 days.
Smart Engineers Reuse
Today, a KST sensor can last about a year with only three AA batteries, and its accuracy is on par with industrial equipment. As this story shows, these accomplishments are possible because the ST Partner learned to use what was available. They were the first to recommend using a Nucleo board instead of customizing everything. They immediately jumped on the ST drivers instead of updating their own. They used the ST schematics and attended ST webinars to learn about low-power modes and other features. It’s a lesson that too many engineers overlook, but reinventing the wheel won’t help design a faster car.
Meaningful Innovations Bring Solutions
Because KST used all tools at its disposal, it could innovate in meaningful ways. For example, the engineering teams started with ST schematics but worked to optimize it by dropping the LDO for a more efficient solution. KST also learned to improve performance by understanding what customers needed. That’s how the company learned to apply smudge correction or improve calibration. Ultimately, it’s about developing a solution, not a product. It’s about listening to and understanding the problem and how the customers will get their return on investment.