The LIS2DTW12 is the first Micro-Electro-Mechanical System (MEMS) in the industry to embark both an accelerometer and an absolute thermometer. Until today, designers had to use two different devices if they wanted to sense motion and temperature, which increased costs and complexity. Moreover, despite the additional sensing element, the LIS2DTW12 is still part of our “femto” family of low-power devices, which means that it uses as little as 50 nA in power-down mode and only 1 µA in low-power mode. The packaging is also identical to the more traditional LIS2DW12 at just 2 mm x 2 mm x 0.7 mm, meaning that the additional sensor does not necessitate a compromise in power consumption or size, making the LIS2DTW12 an even more attractive proposition.
The majority of MEMS on the market today have a temperature sensor inside their package. However, it’s, in essence, a relative temperature sensor that measures a Vbe, meaning the voltage between a base and the emitter of a BJT transistor, to determine the delta between a value set on the manufacturing line and the current measurement. Devices then use this relative temperature to calibrate the measurements from the motion sensor thanks to a compensation mechanism. The LIS2DTW12 is a lot better than what’s standard in the industry because unlike all the other MEMS, its sensing module can accurately track temperatures, significantly increasing its usefulness and enabling engineers to use one device instead of two.
2-in-1 and ±0.8 ºC Accuracy
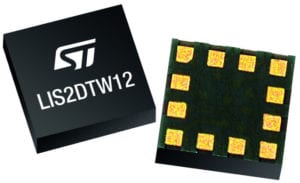
Beyond the simple presence of an absolute temperature sensor, we also see that its performance opens it to a wide range of applications. It can sense temperatures from -40 ºC to +85 ºC and offer a 12-bit output with a typical accuracy of ±0.8 ºC between 0 ºC and 70 ºC and a precision of ±1.3 ºC when it comes to more extreme measurements. Discreet temperature sensors tend to have a ±0.5 ºC accuracy, which means that the compromise in performance from this two-in-one solution is minimal and it can satisfy the needs of a tremendous range of applications that won’t notice a loss of ±0.3 ºC in precision. Whether it is for the transportation of flowers, medications, consumer goods, or other industrial scenarios, the reduction of the bill of materials and the design simplification will offer returns that will easily overshadow this slight loss.
To reach such levels of precision, we changed our testing processes and found clever ways to calibrate the temperature sensor. Indeed, we test the accelerometer at one standard ambient temperature, which means that there aren’t any environmental changes enabling the calibration of the thermometer itself during that time. However, by controlling every aspect of the manufacturing process, including the ambient temperature at various facilities, we can bypass this initial challenges to calibrate the temperature sensor properly and offer a unique two-in-one solution that is extremely close to a discreet thermometer.
Same Packaging and Power Consumption
The other feat of engineering that our teams accomplished when they designed the LIS2DTW12 resides in the fact that the addition of the temperature sensor didn’t require additional space. As is the case for all accelerometers, the new device uses an application-specific integrated circuit (ASIC) that serves in part for the calibration of the motion sensor. By using available space on this ASIC as well as standard transistors, we were able to add the components that enable the system to measure absolute temperatures, without requiring any additional space. In the age of IoT, it means the creation of tracking modules that are smaller and simpler to build.
Similarly, the thermometer has an imperceptible impact on power consumption. At equal levels of precision, the LIS2DW12 (without the thermometer) and the LIS2DTW12 (with the thermometer) exhibit the same levels of power consumption. It is also possible to shut the thermometer down and only use the accelerometer, enabling designers to tweak the component’s behavior to increase the system’s efficiency further. Developers can thus conceive a system that will wake the thermometer at certain intervals, or when the device detects motion. Additionally, there are also stationary and motion detection functions to either shut down or rapidly wake up the device after certain events, to further optimize the power consumption.
What Will Be Your Journey with the LIS2DTW12?
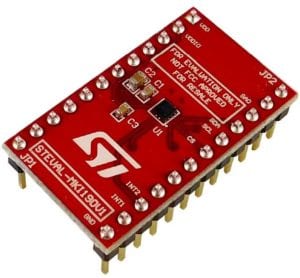
The STEVAL-MKI190V1 evaluation board
The history of the LIS2DTW12 reflects its role in the industry. The component was first a request from companies in the shipping industry that needed a tracking module that could sense motion and temperature while lasting five years on a button cell. The goods they were transporting were sometimes temperature sensitive, and they needed to have a thermometer that could offer new guarantees to their customers while still meeting extremely tight power constraints. The device we came up with was so successful that we ended up releasing it to the public, understanding that there’s a strong demand for smarter integration of sensing elements in a tiny component that consumes very little energy. The new device also shows our teams’ ingenuity and the advantages that come from controlling the entire manufacturing process.
Engineers and enthusiasts can first grab the evaluation board STEVAL-MKI190V1 to experiment with the LIS2DTW12. The device sits on the STEVAL-MKI109V3 motherboard and developers can use the STSW-MKI109W Unico graphical user interface to configure the registers and start writing an application. They can also use it to visualize the device’s output and test its limits by plotting data points. The video below will ensure developers can start their project faster and avoid spending too much time learning about these tools before they can work on their IDE of choice. Designers will also appreciate the fact that the STEVAL-MKI190V1 comes with schematics to help them create their PCB faster.