What happened in 1996? Bill Clinton was re-elected President of the United States. General Motors was the biggest American company. Apple was trading at about 22 cents per share. IBM’s Deep Blue became the first computer to beat the current world’s chess champion, Garry Kasparov. And ST started collaborating with the University of Catania on silicon carbide (SiC) which is transforming electric vehicles today. To celebrate the 25th anniversary of SiC at ST, we decided to explore its role in the industry today, how we got there, and where we’re going. According to a study by Exawatt, 70% of passenger battery electric vehicles will use SiC MOSFETs by 2030. The technology is also transforming other markets, such as photovoltaic inverters, energy storage, power supplies for servers, charging stations, and more. It is thus critical to understand SiC’s journey during these last 25 years to help today’s and tomorrow’s engineers.
Silicon Carbide and How the Industry Overcame Challenges
SiC’s story is fascinating but also fierce because it shows that to be the best, it is also essential to be the first. Silicon carbide’s properties were well established in the early 20th century, with the first SiC LED dating back to 19071. Physicists knew silicon carbide had a wider bandgap compared to silicon by about 2 eV. At room temperature, it meant SiC devices had a critical electric field that could be five to ten times superior. As a result, the new technology could vastly improve conversion efficiency while tolerating higher voltages and harsher conditions.
The Roadblock
The problem was that by 1996 no one knew how to use SiC commercially in a semiconductor fab. The SiC substrate had way too many flaws, and the ovens’ high temperatures were incompatible with the material. Additionally, it took a decade more to manufacture SiC devices on wafers larger than two inches, something essential when bringing costs down. However, by being one of the first to invest heavily in the technology and working with academia, ST managed to solve all these challenges. By May 2002, we showed the first Schottky SiC diode. Then, in 2006, we manufactured SiC devices on three-inch wafers and mass-produced our first generation of diodes in 2007.
The Roadmap
A critical chapter in SiC’s history took place in 2009 when ST sampled its first SiC MOSFET. The milestone is important because it opened the door to significant improvements in power devices. Five years later, we were manufacturing the first generation of SiC MOSFETs. Everything after that followed at a far greater rate thanks to all the work that took place before. By 2017, only three years after the first generation of MOSFETs, ST released a second generation that more than halved the device’s ohmic resistance. And in 2020, we launched our third generation, which perpetuated the trend. ST also moved to six-inch discs by 2016, and we are already looking at producing SiC transistors on eight-inch wafers.
Silicon Carbide and Why It Matters Today
The Best Way to Earn Trust
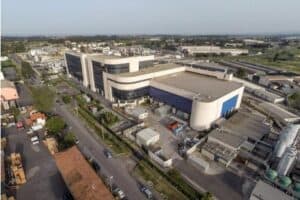
The history of Silicon Carbide teaches that being one of the first to solve fundamental roadblocks matters. By being a precursor in the use of silicon carbide substrates in semiconductor fabs, ST came up with new solutions that led us to produce more and better SiC devices. Today, ST is the first maker of SiC devices in the market. Moreover, our Catania plant is one of the largest SiC fabs in the world with tools capable of transitioning from 150 mm to 200 mm wafers. Hence, early investments in silicon carbide devices now mean that ST can ensure stable supplies regardless of volumes.
ST currently manufactures its flagship high-volume SiC products on two 150-mm wafer lines in Catania (Italy) and Ang Mo Kio (Singapore). However, assembly and test operations take place in its back-end sites in Shenzhen (China) and Bouskoura (Morocco). Through STMicroelectronics Silicon Carbide A.B. (formerly Norstel A.B., which ST acquired in 2019), our goal is to source more than 40% of our SiC wafers internally by 2024 while acquiring the rest from other suppliers.
The Virtuous Cycle
Being first also created a virtuous cycle. As ST solved problems and manufactured more devices, we got to work with the companies that used our devices. For instance, we saw rapid adoption of our SiC products in new and popular electric vehicles. As a result, it allowed us to witness our products in the field and talk to companies about their experience. In return, it enabled us to optimize our processes further and improve electrical performance to release more efficient and robust models, leading to greater industry adoption, thus continuing the cycle. Today we are shipping SiC MOSFETs rated at 1,200 V with a resistance of 3.3 mΩ x cm2.
Silicon Carbide and What Engineers Should Expect Tomorrow
Si, SiC, and GaN
Looking at the future of Silicon Carbide, engineers must consider the larger context of wide bandgap transistors. Indeed, with the advent of gallium nitride, how should designers view SiC? The answer lies in each of the material’s electrical properties. Just like SiC doesn’t replace silicon, GaN is not a substitute for SiC. There may be some overlapping, but in most applications, each material enables new designs, thus complementing the other. ST’s leadership in SiC through the past 25-year history not only led to 70 patents but is a testament to the fact that the new technology doesn’t threaten silicon at all. Indeed, while we developed new SiC devices, ST’s IGBT portfolio still featured new products and innovations. Moreover, we recently celebrated 20 years of superjunction STPOWER MOSFETs with the many industries that favor these devices over SiC.
Today’s and tomorrow’s engineers must understand the role Si, SiC, and GaN play in the industry. For instance, SiC shines in traction inverters or in-car DC-DC converters with a bus voltage of either 400 V or 800 V requiring 600 V and 1,200 V MOSFETs, respectively. Additionally, SiC is easier to drive, it currently tolerates higher temperatures than GaN thanks to its thermal properties, and traction inverters don’t benefit from gallium nitride’s higher frequencies, which pushes designers closer to SiC. On the other hand, teams are currently using GaN at lower voltages (between 100 V and 600 V). Furthermore, in some industrial or consumer applications, GaN’s faster-switching speeds significantly impact efficiency. Similarly, Si remains the better choice when companies don’t benefit from the better efficiency afforded by GaN or SiC.
The Next Chapter
After 25 years, Silicon Carbide is entering a more mature stage. As a result, the industry won’t see ohmic resistance decrease as drastically as before, but it will see more robust devices. Costs will also continue to decrease as ST fabs experiment with larger wafers and new processes. Indeed, we are investing in SiC substrate technologies to improve quality and optimize production. As a direct result, the industry can expect improved yields and lower costs, thus pushing SiC into more designs. Hence, after 25 years, SiC is entering a new era of democratization and transformation.
- For more information on SiC’s inherent properties, check out our blog post entitled “Silicon Carbide in Cars, The Wide Bandgap Semiconductor Revolution”
- Casady, Johnson, Status of silicon carbide (SiC) as a wide-bandgap semiconductor for high-temperature applications: A review, doi:10.1016/0038–1101(96)00045–7 ↩︎