ST’s first evaluation board serving as a flight controller unit for toy drones, the STEVAL-FCU001V1, is making its public debut at the Rome Maker Faire that will take place between December 1st and December 3, 2017. To make the demo even more meaningful, we’ll give away 15 kits containing all the parts necessary to fully assemble a drone and start using the new board in no time. We also invite everyone to attend a lecture in Italian, during the event, that will go over the new unit and the basics necessary to understand drone design. We also welcome attendees to our booth and invite them to ask questions to the engineers and teams present on the show floor.
Indeed, the point is not merely to show a new product but offer a significant contribution to the community. Hence, ST is providing the board’s firmware on GitHub and opening the entire source code to encourage students, engineers, and enthusiasts to modify it and share their ingenuity. Furthermore, we’ll also provide a bill of material for the kit and even give out the files to print the frame using a 3D printer, so those that can’t get their hands on it can still obtain the parts quickly. It’s a different approach than what ST does typically with its firmware or function packs, but what drove us was this desire to impact people’s lives, which explains a lot of the design decisions that went into the STEVAL-FCU001V1.
Why Use ST MEMS to Fly a Drone?
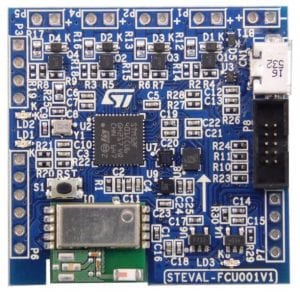
MicroElectroMechanical Systems (MEMS) are at the heart of flight controller units since they track the drone’s movements. The current firmware of the STEVAL-FCU001V1 relies on the 3-axis accelerometer and 3-axis gyroscope LSM6DSL, the same component found in step counters and virtual reality headsets, among many others. Indeed, the current ST firmware doesn’t need another sensor to fly the drone, which is a testament to its accuracy and reliability. Engineers designing a drone often wonder which MEMS to choose and they must regularly test their prototypes in the field to see if a part is adequate. The challenge is that specifications alone don’t capture how a sensor will behave in a high vibration environment, like that of a drone. However, by using the STEVAL-FCU001V1, and the tried-and-true LSM6DSL, designers already know that they have a part that fits such an application.
However, ST wanted to impact the lives of students and enthusiasts by giving them a lot more than what the minimum required. Hence, the STEVAL-FCU001V1 also includes the LPS22HD, the best pressure sensor ever put on a drone thanks to its vertical resolution of 8 cm (3 in) and its acquisition rate of 200 Hz. As a result, a program using the sensor’s data could determine the drone’s altitude and maintain a hovering position without manual intervention, as well as record the device’s ascent and descent speed to prevent crashes. Furthermore, the unit also uses the LIS2MDL magnetometer so even if there’s no complicated GPS system on board, developers can write a routine allowing the drone to come back to its original position by only using the component’s output. Indeed, the STEVAL-FCU001V1 is all about enabling engineer’s creativity by giving them even more possibilities.
How to Help Developers?
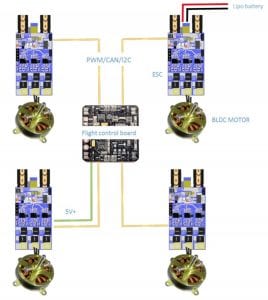
This design flexibility also explains the presence of the STM32F401CC microcontroller (MCU) that drives the entire board. The reason ST chose this component was to make developers’ tasks more manageable. Indeed, this is one of the most popular MCU from our family of products. As a result, users benefit from a fantastic community and vast resources that will assist them in developing their application. Furthermore, it offers impressive scalability. Teams that want to build a smaller application can start on the STM32F401 then scale down to another ST MCU while reusing a lot of their original code. On the other hand, the extra power available signifies that they can also work on new features without the fear of running out of memory, thanks to its 256 KB of Flash. Engineers can also access many communication interfaces to more easily add sensors, facilitate developments and debugging, or use other RF modules.
Similarly, because ST’s goal was to offer more features than what users have come to expect, we also included the STC4054 battery charger, a type of component that isn’t common on flight controller units for toy drones. Rated at 800 mA, the device can charge a one-cell Li-Po battery while the board is connected to a PC via a USB cable for instance. The STEVAL-FCU001V1 thus becomes quite practical for developers who can use their drone right after debugging it, without worrying about the state of the battery.
What’s Your Next Big Thing?
Now that the board is public, we can’t wait to see what you will do with it, how you will use the pressor sensor and magnetometer, and what other features you will develop. Will you include a Time-of-Flight sensor, like the VL53L0X we delved into during our Developers Conference, to program an anti-collision system, or will you add another motor driver for a gimbal? In any case, an Android application, currently in beta, will not only help students design mobile software to control the drone but also collect data from all the sensors, so developers can more rapidly start developing routines to take advantage of the board’s resources.
The STEVAL-FCU001V1 is currently available for purchase at major distributors for about US$30, and ST is also making available an electronic speed controller, the STEVAL-ESC001V1, to drive bigger propellers. Come and visit us at the Rome Maker Faire to see the new flight controller unit in person and leave us a comment below to tell us what features you think the drones of tomorrow will have.