Let’s discover the three winning projects of last year’s National University Embedded Chip and System Design Contest. ST was one of the sponsors of this national competition in China, and the three projects that took first place in 2022 used an STM32 microcontroller. ST platforms do well in those events because we collaborate with institutions of higher learning through our ST China University Program. We realize the importance of working with the next generation of innovators and strive to give them the tools, expertise, and solutions they’ll need to do their best work.
That’s why ST also collaborates on curriculum, training initiatives, labs, and talent programs. The Chip and System Design Contest is just one example. Additionally, we have nurturing programs, conferences, and even host contests to increase our positive interactions with teachers and students. It’s all about making our technology more accessible in China. Consequently, we thought it was important to highlight the fascinating solutions that came out of the National University Embedded Chip and System Design Contest and how they are making the world a better place.
Intelligent Negative Pressure Wound Therapy
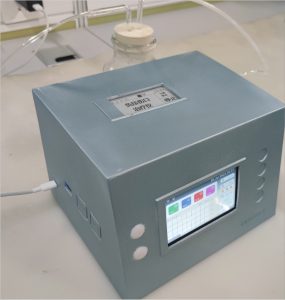
The Nanjing University of Information Science and Technology team worked on intelligent negative wound pressure therapy. Their professor interacts with medical institutions and felt there was a need for such an innovation. In its simplest form, negative pressure wound therapy uses a vacuum or pump to suck the air around a problematic ulcer, burn, or injury that tends to be challenging to treat. The negative pressure tightens the edges for more rapid healing and prevents bacteria growth, thus limiting the risk of infection. The three-member team working on this project started from scratch and spent three months developing their product. One member focused on the 3D-printing, another worked on microcontroller programming, and one tackled the design circuit.
The whole thing runs an STM32L4R5ZI, including the logic, the 4.3-inch display, and the UI. The program takes data from a thermometer, barometer, and hygrometer, among other sensors, to provide critical information to the medical staff and ensure greater pressure stability. As the student explained, given their constraints, the ST Hardware Abstraction Layer, the STM32 ecosystem of tools, localized documentation, and the STM32 community enabled them to work faster. They also found the right amount of memory and peripherals to run all their modules in the ST MCU and used ChromART to optimize the display of UI elements. There are even mobile and PC apps that help visualize the information captured.
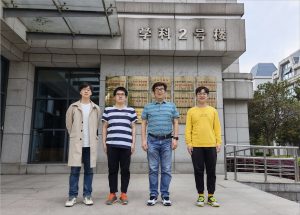
The professor will continue to work on this project with subsequent classes. Due to the medical nature of the product, many regulatory approvals are still required before anyone can think of mass production. Regardless, the students accomplished something remarkable by showing that it was possible to create a negative pressure machine for wound treatment with mobile and PC applications that aren’t common for this type of device, making it easier to use in a non-hospital setting.
Industrial inspection helmet embedded with thermal imaging
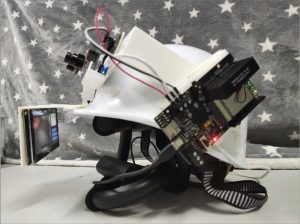
The inspection helmet by Wu Buwei, Wang Junyi, and Xiao Pengliang from Anhui University is an excellent example of computer vision using embedded systems. The headwear contains two modules: a camera and a display. The former captures images and sends them to a board running a machine-learning algorithm that recognizes objects and shows the results on a screen. More specifically, the application can track three hand gestures: a fist, an OK, and a tick. It also tracks motors and their temperatures by singling out the motor within a frame. The application thus opens the door to detecting more complex objects and new interactions with interfaces thanks to hand motion detection.
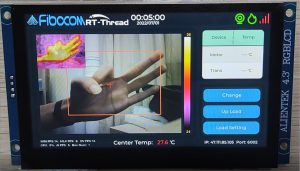
It’s the only project with a strong machine-learning push. The team first took over 400 pictures and labeled them. The students then used YOLO to train their neural network before converting it into MCU code using STM32Cube.AI. It enabled them to work with lightweight tools and create an accurate machine-learning application that could efficiently run on the STM32H750 ART-PI development board. Indeed, while starting with an application running at 4 FPS, they reached 20 FPS by optimizing their neural network and code to take advantage of the STM32H7 hardware.
Maximum power point tracking (MPPT) controller
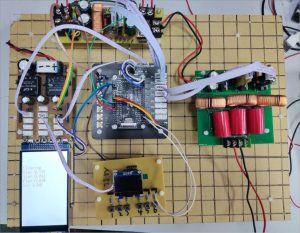
Wang Hao, Yuan Kekai, and Han Naize from University South China created a maximum power point tracking controller. As the name suggests, it tracks the voltage and current of a photovoltaic converter to determine its maximum power output. Knowing when the converter will reach peak power can help adjust operations to reduce losses. Indeed, solar power fluctuates depending on the time of day or other factors. The MPPT tracks the maximum power that can be extracted at a given point and adjusts the pulse-width modulators and DC converters to improve the overall efficiency. Consequently, the MPPT must be accurate and fast to work well.
The university project won first place because it worked on the fundamental aspects of MPPT controllers and improved power generation by 45% by moving from a traditional analog system to a microcontroller. It used an STM32H743 to run the control algorithm and leveraged its high-resolution timer and complex waveform builder to adjust the pulse width modulator, among other things. Put simply, it enabled the university students to benefit from the speed, efficiency, and precision of a digital system. For instance, the MCU’s ADC enabled them to obtain numerous samples rapidly, which is essential when running the algorithm. The students also used the MCU’s watchdog to cope with environmental hazards and improve overall stability.
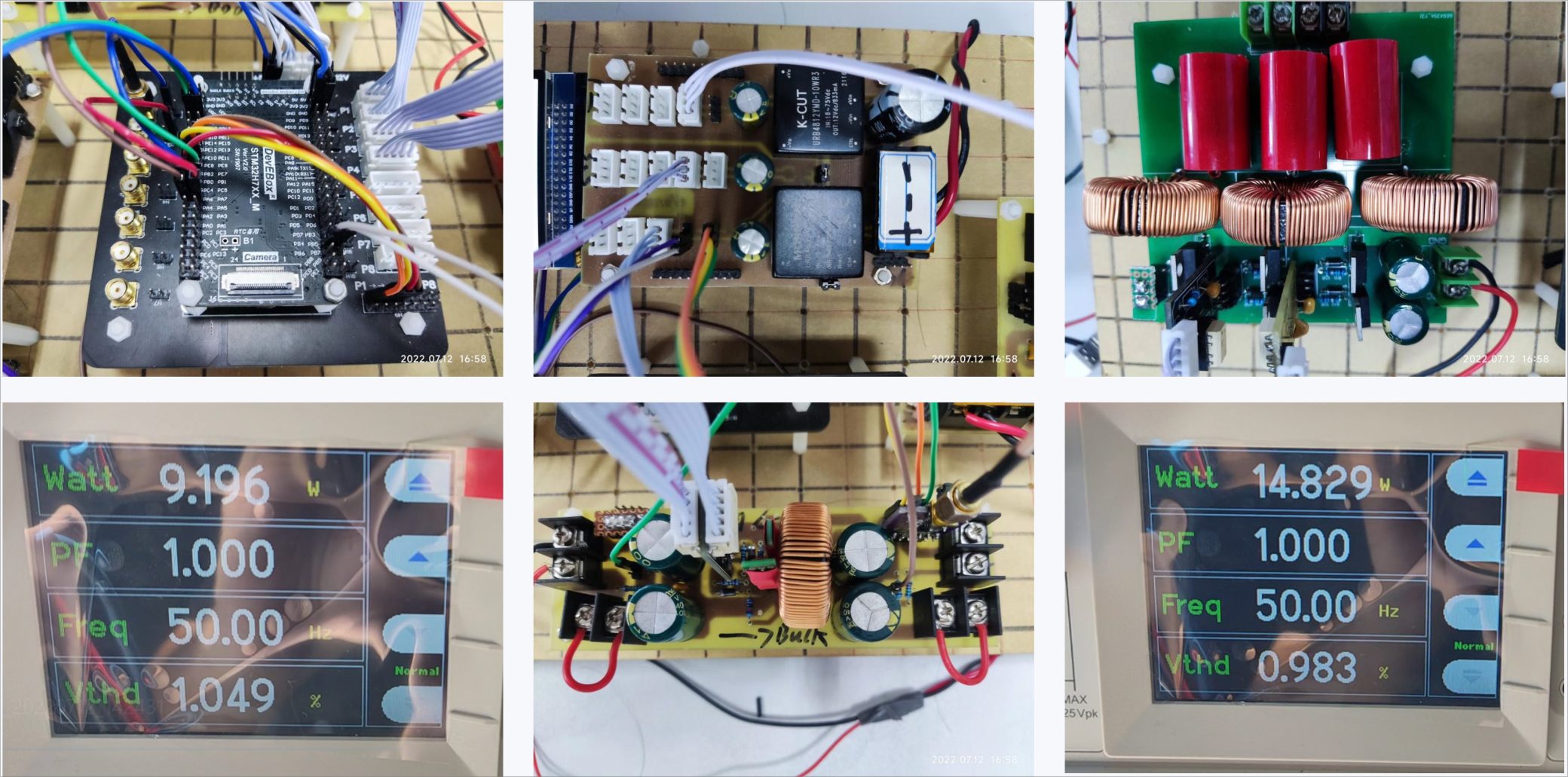