The STSPIN32F0 and the STSPIN32F0A launching today are ST’s first System-in-Package (SiP) combining a three-phase BLDC (BrushLess Direct Current) electric motor driver and an STM32 Cortex-M0 microcontroller (MCU). Whether we are talking about smart industries, drones, or 3D printers, to name a few, motor control is at the center of many of the innovations that are shaping our decade. However, one of the most significant challenges facing engineers is that they must increase their design’s intelligence while shrinking the size of the end products. That often means adding more components to augment the computational throughput, while making boards smaller and electrically more efficient.
Hence, the STSPIN32F0 and STSPIN32F0A are truly unique solutions to overcome such trade-offs thanks to their tiny 7 mm x 7 mm packages, which house an analog and a digital IC.The fundamental implication is that the intelligence is now closer to the motor and independent of the central computational unit. As a result, the design is far more flexible and autonomous, which improves its performance and diagnostic capabilities since it can react to external events in real time.
Both motor controls are compelling because they include a three-phase gate driver with 600 mA current sink and source, operational amplifiers, as well as a comparator. On the digital side, ST uses its STM32F031C6, which runs at 48 MHz, and provides 4 KB of SRAM with hardware parity as well as 32 KB of Flash memory for running applications. The device also has 16 GPIO ports and is compatible with some of the most sought-after interfaces today, such as I2C, SPI, and USART. The STM32 MCU chosen is also unique because its temperature range is unusually wide (between –40 ºC and +125 ºC), ensuring that the STSPIN32F0 can work in an incredibly vast number of situations.
Why an MCU?

An ARMv7 microcontroller adds tremendous flexibility to the design. Previously, engineers had to either add an external processor, making their boards more complicated, expensive and power-hungry or accept severe limitations. Thanks to the efficiency and size of the STSPIN32F0 and STSPIN32F0A, they can now have the best of both worlds. For instance, the presence of the MCU means engineers can quickly use vector control (also known as Field-Oriented Control or FOC) without any additional components. This method significantly increases precision and is an absolute must when using sensorless BLDC motors. In a nutshell, FOC uses the currents at the phases to create a reference frame of the stator represented by a two-coordinate system (alpha axis, and beta axis). An algorithm then generates a vector that represents with high accuracy the movement applied to the rotor.
The STM32 MCU found in the STSPIN32F0 and STSPIN32F0A is also vital in implementing security features too often overlooked, and yet of the absolute importance in smart industries. Hacking a robot’s application could massively damage a factory’s operations, causing not only financial but physical harm, for instance. This is why the MCU used offers read and write protection modes for the Flash memory. During production, ST programs the bootloader in the system memory, safekeeping it from tempering efforts. Engineers can then choose the level of protection they are comfortable with by just following the components’ documentation.
How Can the STSPIN32F0 and STSPIN32F0A be so Versatile?
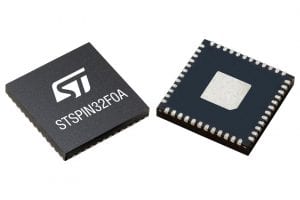
Another reason the STSPIN32F0 and STSPIN32F0A are so impressive is that they can be used in so many different appliances. From kitchen robots to power tools, from portable vacuum cleaners to hand dryers, or from coffee machines to industrial applications, their analog IC is designed to tolerate a wide range of use cases. For instance, the STSPIN32F0 can accept an operating voltage as low as 8 V or as high as 45 V. On the other hand, the STSPIN32F0A has an operating voltage of 6.7 V, which makes it suitable for battery-powered applications the equivalent of two LiPo (Lithium Polymer) cells. Furthermore, both can output 3.3 V when using a DC/DC buck converter, and 12 V when using an LDO linear regulator.
Aside from the different operating voltages, the STSPIN32F0 and STSPIN32F0A vary in their operational amplifiers (op-amps). The former uses four rail-to-rail op-amps and a dedicated decoding logic to support motors using analog Hall-effect sensors. On the other end, engineers who know their designs will never need analog Hall-effect sensors can gravitate toward the STSPIN32F0A. Its three rail-to-rail op-amps will offer all the signal-conditioning they need for sensing the current at the shunt resistors.
Many Security Features Baked In
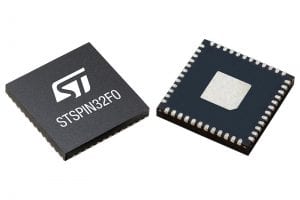
The STSPIN32F0 and STSPIN32F0A are also full of features aiming to protect the system against a malfunction, regardless of the application. For instance, thermal sensors next to the DC/DC and LDO regulators trigger a shutdown if they are overheating. Similarly, the analog IC integrates a comparator guarding against over-currents, and it’s possible to use the MCU to set the current threshold to adapt it to a particular use case. Finally, there’s an Under Voltage Lock Out (UVLO) protection on all the power supplies. This is particularly important in battery-operated devices because a failure to quickly adapt to the source’s low levels could damage some of the components.
Furthermore, the STSPIN32F0A is also introducing an on-chip bootloader accessible via the serial interface. Its presence means engineers can either download or upload their firmware while on the field to either add a feature or correct a bug on the fly, making any patch or upgrade deployment a breeze. Furthermore, if teams end up designing a connected device, they can implement over-the-air updates. Hence, if there’s a security breach, the maintenance crew can more quickly respond to the vulnerability.
The ST Ecosystem
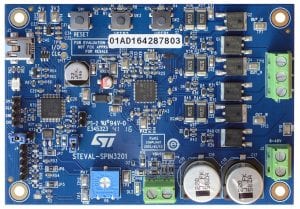
To help developers jump-start their prototypes, ST came out with the STEVAL-SPIN3201, an evaluation board that houses the STSPIN32F0, and the STEVAL-SPIN3202, which includes the STSPIN32F0A. Both also use the STD140N6F7 MOSFETs. This is a tremendous advantage over the competition, because instead of having to come up with a board first, then start developing for it, engineers can work on their application right away and more quickly adapt their final design using fewer iterations, which reduces the time to market. Furthermore, the ST-LINK-V2 ensures that all debugging operations and firmware uploads to the board only require linking it to a PC using the USB connector provided.
ST also goes way beyond its competitors by offering an open-source version of its Field-Oriented Control algorithms in the form of the STSW-STM32100 SDK. Hence, not only does the STSPIN32F0 and the STSPIN32F0A make it easy to implement vector control, but things are even more straightforward because developers have access to the implementation itself. There’s also an open source firmware example for the STSPIN32F0, the STSW-SPIN3201, with precompiled binaries to ensure teams can start testing the board without entering a single line of code. The software includes a graphical user interface, so engineers can just key-in the parameters of their device and automatically generate header files.
Finally, ST is also launching the STSW-SPIN3202 today, a six-step motor driving library for both STSPIN32F0 and STSPIN32F0A. Hence, thanks to the ST ecosystem, the two components are much more than impressive BLDC drivers; they are changing how professionals and enthusiasts shape the products of this generation.