Time-of-Flight (ToF) sensors are often under-appreciated, which is why John Kvam from ST will hold two lectures at the next Developers Conference that will take place in Santa Clara, California, on September 6, to introduce them and explain how to optimize products around them. When people hear “proximity sensor”, they most often think of smartphones, laptops, or automated taps in public washrooms, but there are a lot more applications that already benefit from these inexpensive and accurate solutions. Engineers have placed Time-of-Flight sensors in fascinating devices, like the bottom of drones to facilitate landing operations, or on artificial legs to simplify obstacle detection, and they have found new applications in AR and VR, as other presenters at the Developers Conference will attest. In many cases, they have replaced complex, expensive, and inelegant workarounds thanks to a simple, inexpensive, and precise sensor that is quite easy to program and integrate.
Understanding Time-of-Flight Sensors
Very simply, a ToF sensor will send a laser, wait for it to bounce off a surface, and use the time it took the light to travel back and forth to determine the object’s proximity, something that ST calls FlightSense. Hence, a Time-of-Flight sensor has two major components: an emitter and a receiver. The emitter is often a VCSEL (Vertical-Cavity Surface-Emitting Laser), which uses mirrors to emit a light perpendicular to the surface of the die. In general, lasers come from a quantum well made of gallium arsenide (GaAs) and aluminum gallium arsenide (AlGaAs) to produce light with a wavelength ranging between 750 nm and 980 nm. VCSEL has many advantages, such as the ability to more quickly focus on a particular wavelength, and test the laser at the wafer level to reduce production costs.
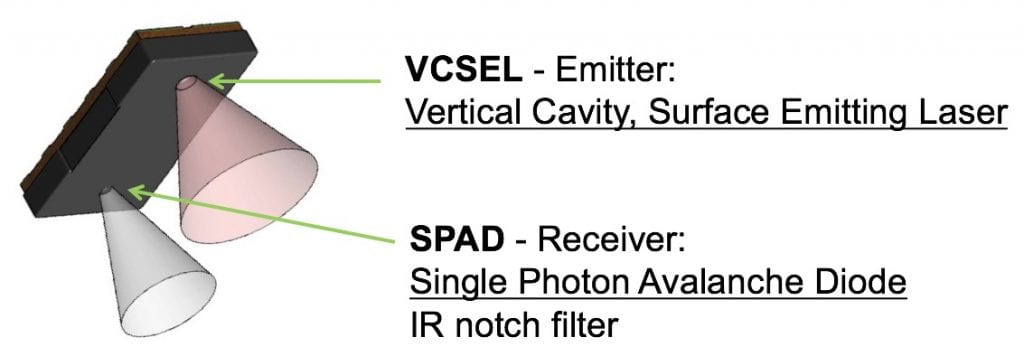
To detect the photons coming back to the ToF sensor, ST uses a Single-Photon Avalanche Diode (SPAD). As the name suggests, this component contains a photodetector so sensitive that a single photon can trigger an avalanche current. Hence, during normal operations, the VCSEL sends light at regular intervals. When the SPAD starts to get a response, a system inside the sensor increases emissions by sending millions of pulses of light every second, while the processor measures the current from the SPAD to average the number of photons that came back and the time it took them to do so. The result is a value that determines the proximity of the surface reflecting the laser.
VL6180X and VL53L0X: It’s All About Power and Range

To better understand ST’s family of sensors we sat down with John Kvam who joined the team behind those components more than a year and a half ago. As an application Engineer at ST for more than 10 years with extensive knowledge in embedded systems, he doesn’t hesitate to compare his work on ToF sensors to a “religious experience”, which is quite fitting because you won’t find someone with more zeal, conviction, and passion. Hence, it’s pretty much a guarantee that he will make converts out of his listeners.
As John explained, ST has two major ToF sensors: the VL6180X and the VL53L0X. The former has an official range of only 10 centimeters (four inches), although the firmware can be tweaked to detect objects as far as 40 cm (almost 16 in), and its 850 nm laser makes it an excellent solution for low-power applications, while its I2C interface greatly simplifies its integration. On the other hand, the latter demands more power, thanks to a 940 nm laser, but it has a range of up to two meters (6.6 ft) and can more easily bounce off different colors and textures. It’s also the smallest Time-of-Flight sensor in the world. Finally, ST has already announced working on a new ToF sensor, the VL53L1, which allows for multi-object detection and multi-zone scanning.
Seeing the World as ToF Sensors
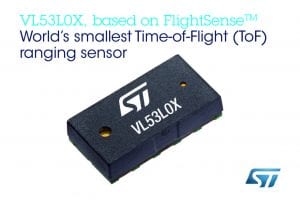
The reason John is also giving a lecture on ToF optimization is that, as he explains, very few people understand the need to comprehensively test their system. The world we see with our eyes is very different from what it looks like at an 850 nm or 940 nm wavelength. As a result, what we think is easily detectable by sensors can sometimes go completely unnoticed, and vice-versa.
For instance, the human eye can easily spot a bottle of water in clear plastic in a well-lit room, but it is entirely invisible to the proximity sensor unless the laser is aiming at the bottle’s label. On the contrary, objects in a very dark environment would still very easily reflect the laser beam, even if they’d be hard to spot by a person. Hence, it’s imperative to evaluate a design and not work on assumptions based on our senses, which could prove misleading.
ToF at the ST Developers Conference
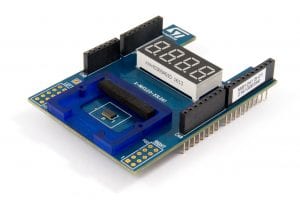
As a result, ST doesn’t only provide the smallest and most efficient proximity sensors in the industry, but the most comprehensive development solutions. The X-NUCLEO–6180XA1 and X-NUCLEO–53L0A1 are expansion boards designed to sit on top of a NUCLEO board to immensely facilitate prototyping. The boards are very inexpensive, which makes testing a breeze. ST also offers free software packages, like the X-CUBE–53L0A1 and X-CUBE–6180XA1, which include drivers, middleware, source codes, application examples, and APIs to help developers build apps quickly. There are even binaries to ensure that testing a program is as easy as dragging and dropping a file onto a volume. Finally, STSW-IMG006 is a Graphical User Interface for Windows that helps visualize the data coming from the VL53L0X to better understand the component’s measurements and build pertinent software around the results.
John Kvam’s two presentations are “Introduction to ST’s Time of Flight Technology: FlightSense”, and “Optimization of Time-of-Flight based products.”
To attend them and learn more about the incredible opportunities afforded by ToF sensors, register for the ST Developers Conferences while tickets are still available.